-
Headquarters -
351 Passmore Avenue, Toronto, ON M1V 3N8 Canada
-
Year established -
1972
-
NAICS -
333519 - Other metalworking machinery manufacturing
-
Major expansions -
2013
-
Employees -
200
-
Exports -
US, India, EU, Asia-Pacific
-
Download -
Samco Machinery
Samco Machinery is a global innovator in producing roll forming machinery and custom built material handling solutions. In business for over 45 years and maintaining ISO 9001 certification, our services include: consultation, engineering, installation, training, commissioning, ongoing maintenance, support, and parts.
Companies that value their employees and their ideas often go far; this is certainly true of Scarborough-based Samco Machinery (Samco). Samco was founded in 1972 by Joe Repovs in a 200-square-feet facility in the Greater Toronto Area. After a number of moves, the company settled in its current Scarborough location: a massive manufacturing facility that occupies 164,000 square feet and includes 9 cranes with capacity up to 25 tonnes. It also operates a facility in India, which opened in 2008 to go further into and meet the needs of the Indian manufacturing market and significantly expanding Samco’s global reach. As Samco’s chief executive officer, Bob Repovs (Joe’s son) continues to lead the firm towards further success and growth.
Samco makes machines used by other manufacturers for their design, engineering, and building needs—and in particular, anything that requires roll forming, or the bending of metal sheets and coils. The company sees itself as an engineering and value-added solution firm, as well as a high-quality manufacturing company. Samco not only builds the desired machines and equipment but will help its customers design and develop the machinery needed for almost any type of project in their industry. The firm produces and sells items for a large variety of industries, including the automotive, energy, storage, HVAC, garage door, building and construction, aerospace, and electrical distribution sectors. Most of Samco’s customers are tier-two manufacturers that use Samco machines to manufacture their own products (e.g., shingles for roofing, bumpers for major auto manufacturers, solar panel racking, highway guardrails, department store shelving, metal framing for buildings, and many other metallic objects used in manufacturing). Samco does sell some secondary goods directly to customers, but it is mainly focused on producing the machinery and engineering solutions that will be used to make the secondary goods.
While Samco offers a wide range of services and engineering solutions its speciality and largest growth potential is its rolling division. As with all their products and services, Samco brings an unmatched level of service and care with their rolling services and products, with the automotive, solar and speciality products as well as a wide array of other industries. What makes Samco so unique is that they work with their customers for literally every step of the process. They use their engineering resources to identify potential forming issues, before production, achieving significant cost and time savings for the client. They provide designs, engineer the product, source the necessary raw materials, production and if needed even the logistics, shipping and final setup. Furthermore, Samco sets deadlines, tests and ensures quality, and is in constant communication with customers at every step in a project’s lifetime. Because of being at every stage of development and production, the rolling division is able to be incredibly specialized, dealing with nearly any rolling related issues across almost all manufacturing industries. This customizability of products and services also comes from having a highly skilled team that does not need to rely on much automation. But, the rolling division at Samco does use the most state of the art technology, particularly in engineering design, simulation and testing. Overall, this boutique nature of Samco’s rolling division in conjunction with the team’s experience and use of advanced technology makes them the ideal firm to work with. It also means that they can adapt to and take advantage of new growing types of manufacturing. For example, solar is becoming an incredibly important global power source that is likely to grow in importance over the upcoming decades. Samco has been able to adapt to this to produce products and provide services to the solar industry.
Like many manufacturers, Samco creates machines using an increasing emphasis on automation to improve both production capacity and overall quality. However, Bob stresses that Samco employees are more important than its automated processes because they are the ones ultimately responsible for the finished product. The words “People, Products, Passion” are proudly displayed in Samco’s facility, demonstrating the company culture of respect for those who work at Samco. Furthermore, Samco is proud of the diversity of their employees. One wall of the factory is filled with flags, representing the many nations that Samco employees originally hail from. There are over 30 different flags from all over the world. Further, Bob emphasizes that employees’ ideas are always considered and, when possible, implemented.
Samco employs 200 people, 60 of whom work at the company’s facility in India, while the other 140 work at the GTA location. The company’s culture of respect for employees has helped it achieve an extremely low turnover rate. Bob states that some of Samco’s workers have been with the firm for over three decades (longer than he has been working there!). As part of its employee-centric atmosphere, Samco offers a large lunch room for its employees, equipped with a ping pong table that sees regular tournaments for the staff, as well as monthly barbeques during the summer in order to foster a sense of community.
Bob admits that there is a shortage of the type of skilled workers that Samco needs in Canada and North America. The company has about 30 highly skilled engineers on site, and many other positions require a significant amount of skill and training. Occasionally, the firm works with local post-secondary schools (including York University and Seneca College) to employ and train students, but most of the time, Samco needs employees with the necessary skills immediately.
On top of a significant national reach, Samco has increased its global presence in the last decade with its new manufacturing facility in India. Opened about 9 years ago, Samco India primarily deals with the rapidly growing Indian manufacturing market, particularly in the auto and solar power industries. Samco leverages its own brand as well as Canada’s highly reputable name to help acquire major contracts in the area, including a $3 million contract from Tata, one of India’s major car producers even before they expanded into India in 2008.
Samco, through its facilities in Ontario and India, works with and produces machinery for companies around the world. Samco’s Ontario plant has a large world map hanging in the front lobby, highlighting each country that Samco has worked with in some way—a current total of 34 countries. About 60 percent of the company’s sales come from the American market. Samco does not focus on one-time sales, and instead puts a strong emphasis on repeat business over a prolonged period. This return customer strategy depends on high-quality products and services, as well as positive and sustained relationships. Fortunately, Samco has mastered the skills needed to succeed in these two respects.
An installation and maintenance service to anywhere in the world help ensure a healthy customer-producer relationship, and Samco’s machinery is always of the highest quality to begin with. Furthermore, the company consistently communicates with its customers during active projects. Bob acknowledges the importance following customers’ instructions and designing the machinery exactly to customers’ specifications. Constant innovation is also a necessity to ensure that Samco’s customers have continued reasons to return. As a result, Samco constantly seeks to develop new machinery and techniques based on its customers unique and ever-changing needs. Samco proudly displays many of its major completed projects with a ‘Wall of Fame’ plastered on both the office and factory walls, which continues to grow as time goes on.
Samco also believes in the importance of education in the industry. The firm commissions and publishes articles, videos, and other educational tools relating to its industry, and calls this collection of materials “Samco’s Academy of Learning.” The reason for this venture is to provide clients with the proper resources to understand the roll forming industry so that they can make the right choices about which products and services to invest in, and how to get the most out of their investment. Once again, this initiative confirms Samco’s belief in a strong customer-producer relationship and the company’s commitment to innovation within the roll forming and general manufacturing industries. The Academy of Learning also includes a multitude of interesting videos that go over many of their different roll forming machinery to help better educate visitors to what they do. These resources are available on Samco’s brand new, easy to navigate website (check it out, the link is down below!).
Samco is a large company that is still growing at a rapid pace. Despite its size and significant capabilities, in many ways, Samco still has the appealing features that are more typical of a small operation: a focus on both employees and customers, and the ability to offer a very high level of customization in the products and services on offer. Samco is a perfect example of an Ontarian owned-and-operated company with a long history of sustained success, and a strong potential for further growth.
For more information about Samco Machinery, visit their website.
Published: November 30, 2017
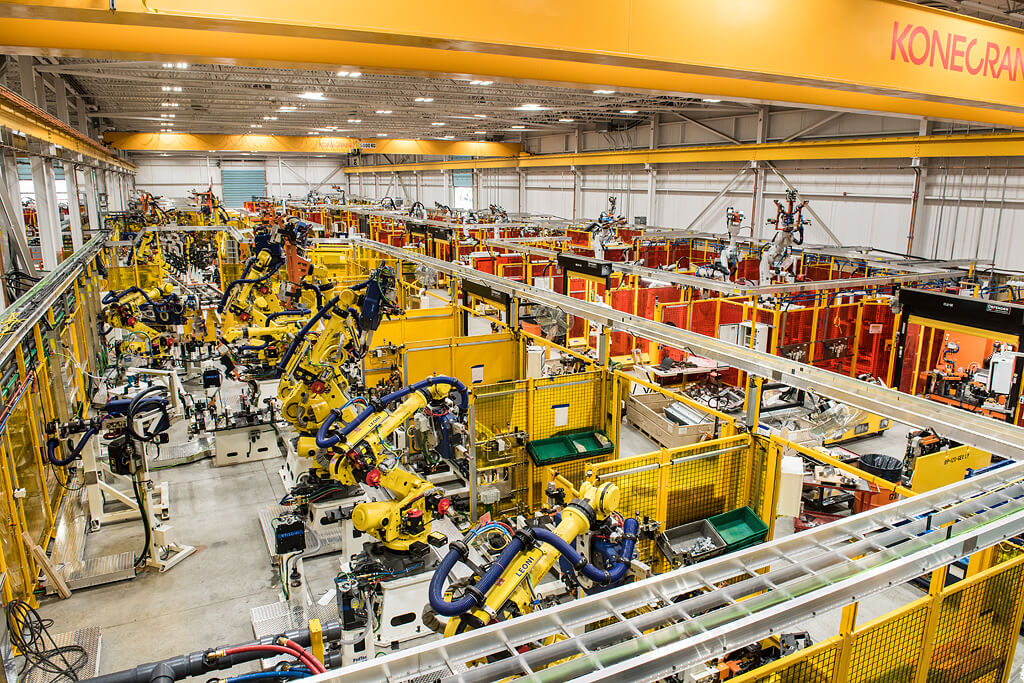
CenterLine
CenterLine is a manufacturer of custom automated welding and assembly lines, as well as resistance welding-related products. The firm is known worldwide as a leader in fastener welding technology, which is used in the production of automotive components.
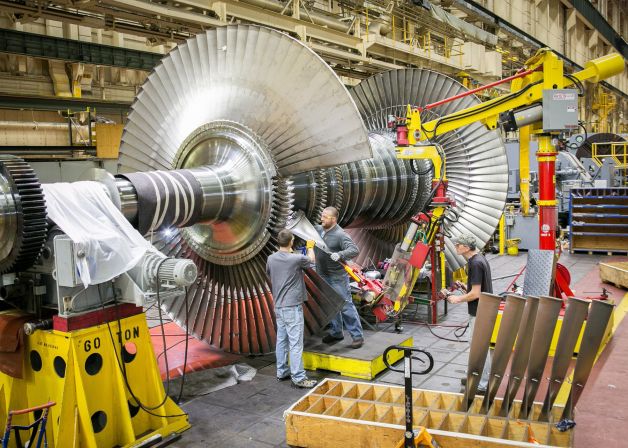
Givens Engineering
Givens Engineering Inc. designs and manufactures light cranes, manipulators and machinery for industrial use. The company specializes in lifting equipment and automated material-handling machines.
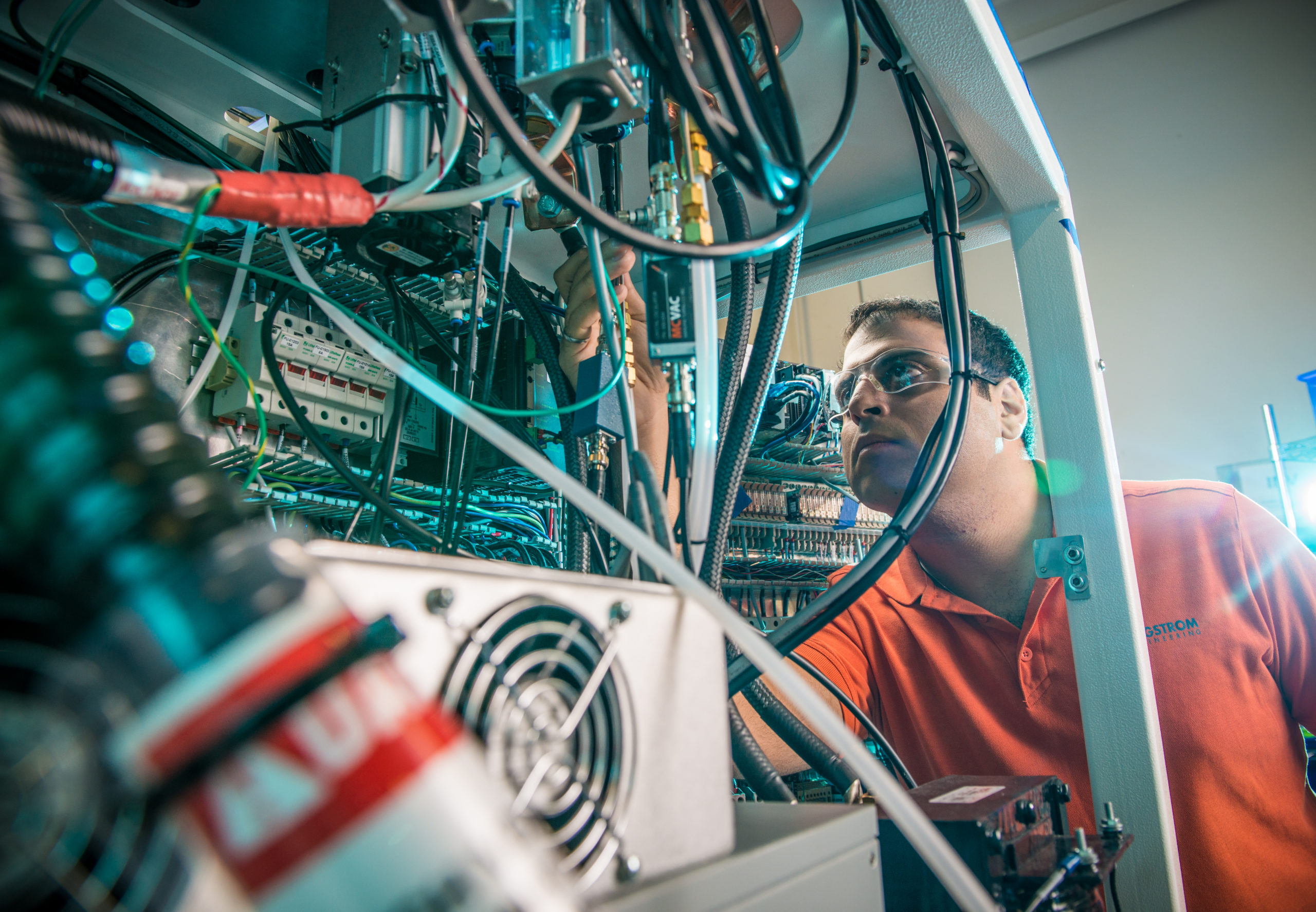
Angstrom Engineering
Angstrom Engineering Inc. is a leading manufacturer of thin film vacuum deposition equipment and vacuum chambers equipment. The firm specializes in designing, manufacturing, selling and servicing machines that deposit thin films, (growing layers of materials on a substrate with thicknesses that can range from less than one nanometer to several microns).
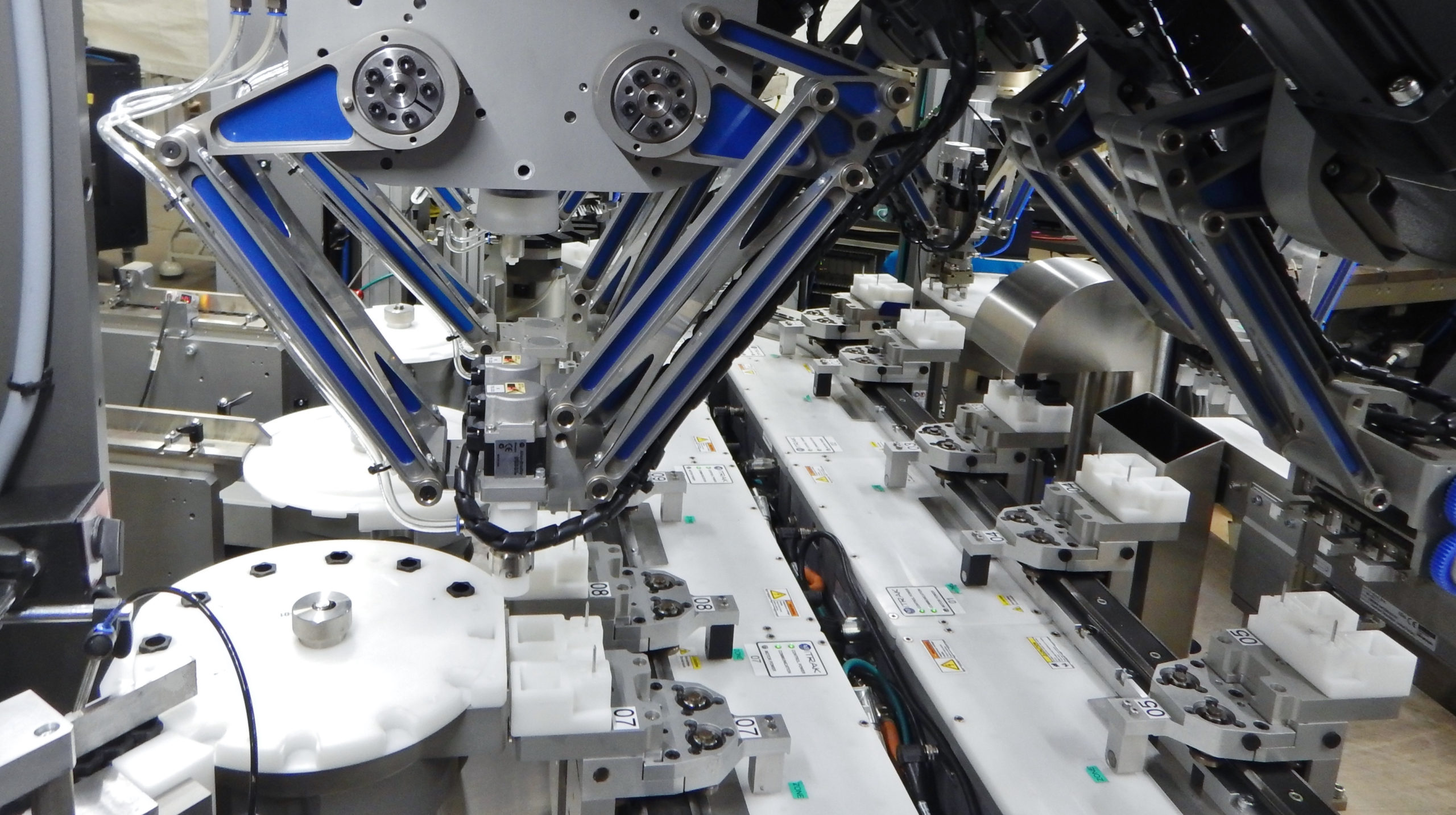
Transformix Engineering
Transformix Engineering is exclusively focused on CNCAssembly® technology in the specialized niche of "continuous motion", and have developed it into a general solution for small-part assembly.
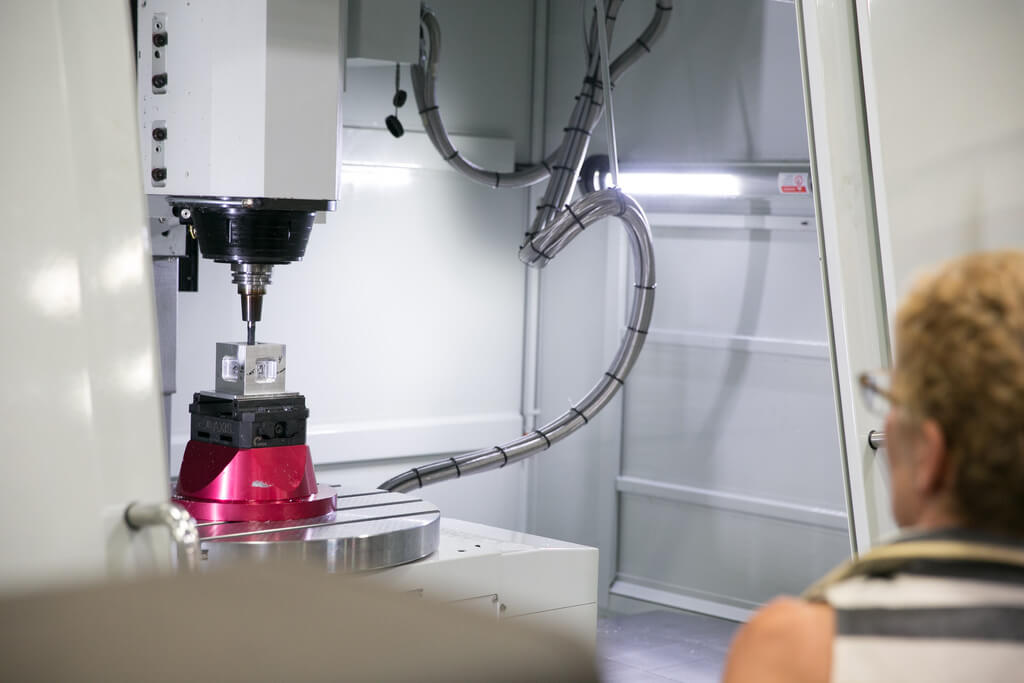
Armo-Tool
Armo Tool is a Tier 2 supplier and provider of “one-stop” precision tooling solutions, from small components to large machines that build Tier 1 parts. It has been family owned and operated since inception.