-
Headquarters -
40 Citron Ct, Concord, ON, L4K 2P5
-
Year established -
2006
-
NAICS -
333519 - Other metalworking machinery manufacturing
-
Major expansions -
N/A
-
Employees -
30
-
Exports -
United States
-
Download -
Prodevco Robotic Solutions
The cutting edge of manufacturing innovation is sometimes literally about cutting edges. Take, for example, the robotic plasma cutting cells developed by Prodevco, a subsidiary of Vaughan-based structural steel fabricator Burnco Manufacturing. Powered by a highly intelligent piece of software, Prodevco’s smart robotic cells automate structural steel fabrication tasks traditionally done manually
“Consensus in the industry is that if you don’t own one of these systems in the next five years, you may be out of business,” Erwin Terwoord, head of business development at Prodevco, says. As Terwoord tells it, steel fabricators need to evolve in order to overcome challenges posed by a tight skilled labour market and raw material supply and price headwinds. “Investing in automation is the most viable option to increase production capacity, reduce costs, bid on more projects and grow,” he says.
Prodevco’s smart robotic cells cut steel pieces, drill holes, and mark weldment locations in a continuous process with minimal oversight. According to Terwoord, the system reduces labour input by up to 90 per cent in complex projects, improves efficiency by a factor of 10, and eliminates defects and material waste. It also saves days of work in complex projects by enabling the direct use of three-dimensional building models for production and eliminating the need to convert them into two-dimensional layouts.
Originally founded in Québec, Prodevco was purchased by Burnco in 2006. The acquisition was strategic for Burnco, whose main line of business today involves manufacturing complex steel building elements for large construction and infrastructure projects. By acquiring Prodevco, Burnco primarily wanted to deploy the robotic plasma cutting technology in its own structural steel operations and boost its productivity. Additionally, the company saw an opportunity to develop Prodevco’s technology further, keep it as a separate business and diversify Burnco’s capabilities and markets. This actually brought Burnco full circle as at its inception in 1994, the company’s main line of business was automation system integration geared for the structural steel fabrication industry.
The overall penetration of this kind of a system among structural steel fabricators is still quite low... About half of larger operations and a much larger portion of smaller manufacturers have not adopted it.
With 30 employees and a capacity to build up to five machines per year, Prodevco is keen to expand its footprint in North America significantly over the next five years. Its product has been installed at about 70 manufacturing facilities in Canada and the United States. Terwoord believes that there is a lot more room to grow. “The overall penetration of this kind of a system among structural steel fabricators is still quite low,” he says. “About half of larger operations and a much larger portion of smaller manufacturers have not adopted it.” Prodevco has been targeting those companies – primarily steel fabricators – through its large third-party dealer network across North America. Entering the European market is also on the horizon thanks to the Canada-European Union Comprehensive Economic and Trade Agreement (CETA).
Through automation, Prodevco’s robotic cells are fundamentally altering how structural steel elements are manufactured. In a typical facility that does not use similar technologies, the first step in a project involves converting three-dimensional digital building models received from designers into two-dimensional layouts through a tedious process. Large steel pieces then go to a workbench. Using the printed layouts and a tape measure, workers would then spend long hours marking down the locations on each piece of steel for each operation such as drilling, cutting and welding. Holes would be made using a magnetic drill. Cutting would be done with plasma or oxyacetylene torches. Weld guns would be used to finally bring everything together. Because requirements for each piece are different and complex, it would take hours to process a single beam, and many buildings may have hundreds of such beams.
Ten years ago this technology was expensive–maybe it was more for larger manufacturers that could afford the initial capital investment required to set the system up. It was exclusive. However, in the past five years, the costs have been coming down and there has been more uptake among smaller businesses.
The simplicity of using a robotic cell contrasts sharply with the complexity of completing these structural steel fabrication tasks manually. An operator needs only to upload the model obtained from the building designer and feed the raw materials into the system. Using a simple interface, the operator then selects the next production part and hits the ‘start’ button. Then the robot takes over and with the help of the built-in software that anticipates all permutations relating to robot movements, starts processing the parts. After measuring and verifying the piece, the robot starts working on multiple operations simultaneously. Here it pierces a hole, there it incises a marking for a weldment, next it cuts the piece in predetermined lengths and shapes. Once it finishes, all workers need to do is to weld the pieces together at the marked locations.
The benefits of installing Prodevco’s system can be a game-changer for smaller companies in the industry, Terwoord says. He explains that a lot of startups in the industry begin their journeys as installers of steel structures in construction projects. After a while, developers and contractors ask these companies to start bidding on new fabrication projects because skilled trades workers are generally difficult to come across. Then, the previously all-manual small shops start evaluating new equipment investments. Terwoord notes that at that point the smaller companies would typically first consider purchasing an automated drilling machine or a bigger saw or a larger angle processing machine. “Now, when they start to look at all the equipment they need separately they see that for a little bit more investment, they can purchase a robotic system that would do it all.”
Labour retention is tough for smaller companies, so more people are evaluating this and thinking that they need this type of equipment to be in this business.
When asked about the affordability of the system Terwoord notes, “Ten years ago this technology was expensive–maybe it was more for larger manufacturers that could afford the initial capital investment required to set the system up. It was exclusive. However, in the past five years, the costs have been coming down and there has been more uptake among smaller businesses.” Terwoord also highlights that the robot adds a production capacity equivalent to a crew of five to 10 workers for a startup. “Labour retention is tough for smaller companies, so more people are evaluating this and thinking that they need this type of equipment to be in this business.”
Adopting Prodevco’s technology can also benefit larger steel fabricators. In addition to productivity gains, they can bid on projects they normally would not because the automated system lowers their labour requirements thus making such projects profitable. That helps them diversify their customer bases and markets. For example, Burnco recently built three thousand tonnes of roof beams for another fabricator that was working on a large warehouse project for a global delivery company. All the beams were fabricated by the Prodevco robot cell at Burnco’s 185,000 square foot facility. “If we didn’t have a robot, we wouldn’t be bidding on that kind of work. We wouldn’t be competitive and actually wouldn’t be able to do that.,” says Terwoord.
Having the flexibility to bid on different types of projects by adopting advanced production technologies can also help fabricators weather unforeseen challenges in raw material markets more effectively, says Terwoord. For example, there was a shortage of roof decks and overhead steel joints as a result of a global supply chain disruption. Only a few large manufacturers made these products. When the supply chain was disrupted, these companies saw a massive order backlog. As a result, construction project lead times increased to a year from the typical two to three months. Many projects were paused. Fabricators that adopted new production technologies, though, had the chance to pivot to working on different projects.
While increased production automation can meet some of fabricators’ needs, it cannot solve every problem, Terwoord acknowledges. Supply issues and labour shortages continue to challenge structural steel fabricators, requiring them to adapt and adjust to new circumstances. Adopting new production technologies can provide a lifeline to companies and give them an opportunity to grow even under such external pressures.
For more information about Prodevco Robotic Solutions, visit their website.
Published: August 29, 2022
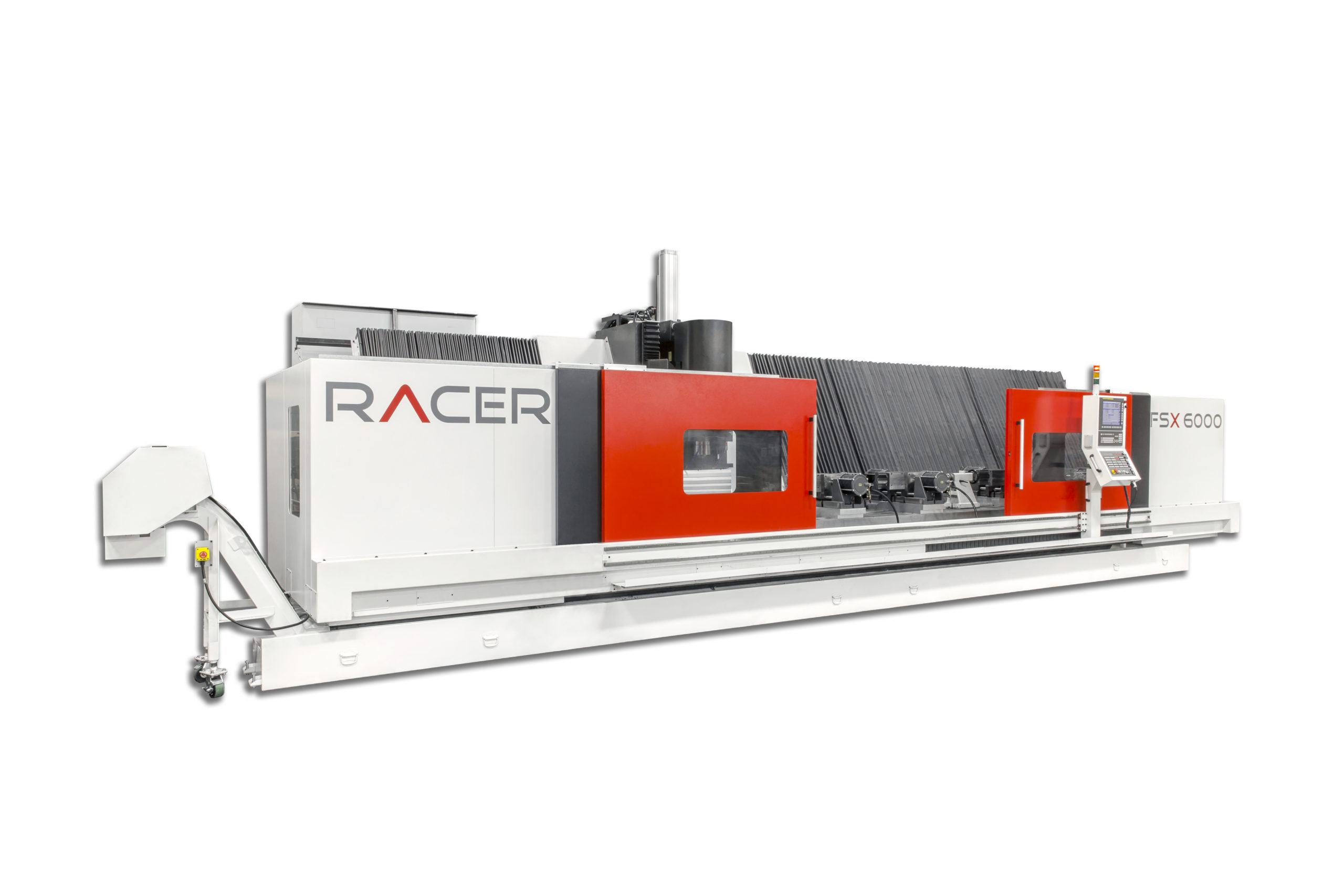
RACER Machinery International
When Siemens North America needed a partner to meet very specific needs for its first digital twin initiative, they chose RACER Machinery International.
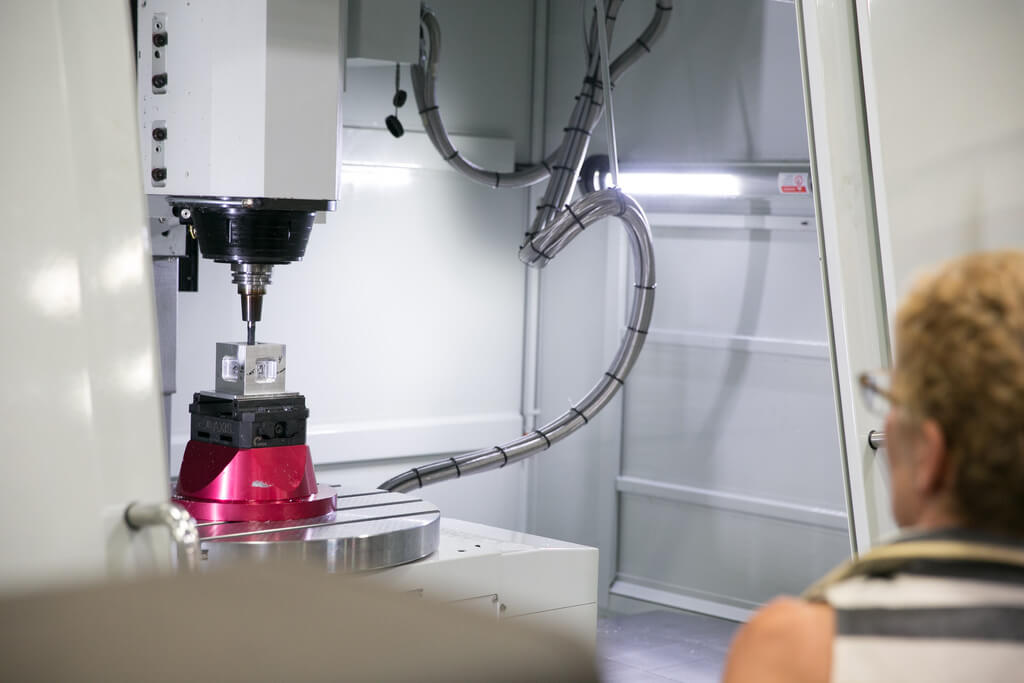
Armo-Tool
Armo Tool is a Tier 2 supplier and provider of “one-stop” precision tooling solutions, from small components to large machines that build Tier 1 parts. It has been family owned and operated since inception.
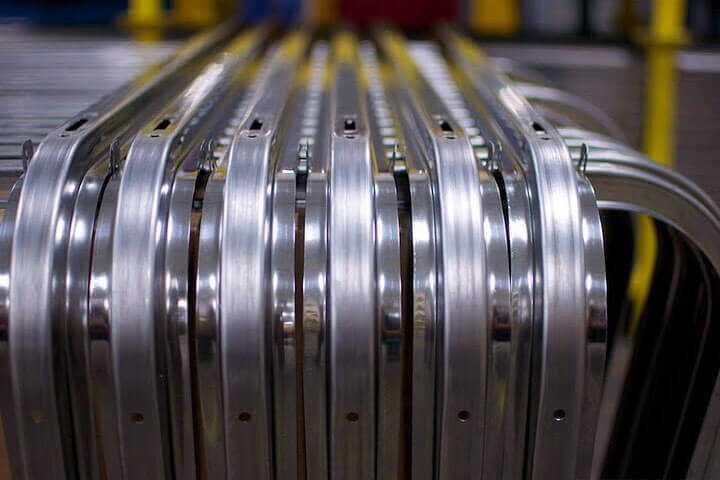
Samco Machinery
Samco Machinery is a global innovator in producing roll forming machinery and custom built material handling solutions. In business for over 45 years and maintaining ISO 9001 certification, our services include: consultation, engineering, installation, training, commissioning, ongoing maintenance, support, and parts.