-
Headquarters -
95 Mumford Rd, Lively, ON, P3Y 1L1
-
Year established -
1991
-
NAICS -
333248 - All other industrial machinery manufacturing
-
Major expansions -
2020
-
Employees -
150
-
Exports -
Global
-
Download -
Ionic Technology Group
Five years of research and development enabled Sudbury’s Ionic Technology Group to launch SafeBox, a product that de-energizes and locks out equipment in a matter of seconds. Today, SafeBox is emerging as the global standard for worker safety in mining and base metal refining.
Equipment de-energization and lockout processes are critical to preventing worker injuries in large industrial sites such as mines and refineries. Even after equipment is shut down and disconnected from a power source, it can restart with the kinetic energy stored in it. This can lead to serious injuries if it happens unexpectedly during maintenance work.
For some of Ionic’s mining and refinery customers, making these necessary processes more efficient without sacrificing safety is challenging. When one such customer approached Ionic in 2016, they hoped to draw on the company’s deep knowledge of safety-focused engineering to address that challenge. Ionic’s response was a technology now dubbed SafeBox, which has emerged as one of the company’s most important sources of revenue.
In a large and expansive operation, what might take as long as 20 minutes can be achieved in a matter of seconds using SafeBox.
SafeBox automates the machine lockout process at mines and refineries with a single-point padlock application. It uses safety-rated technologies to monitor and alert operators for any power left in equipment and machinery, and does not confirm a lockout until all energy has left the circuits. By doing so, it prevents unexpected equipment and machinery restarts, which can lead to worker injuries. In a large and expansive operation, what might take as long as 20 minutes can be achieved in a matter of seconds using SafeBox. That means significant reductions in production downtime in addition to improved worker safety.Global mining and refining companies are already interested in making Ionic’s SafeBox technology their new standard.
SafeBox is only one example of what the capabilities of Ionic’s innovative workforce and entrepreneurial culture can achieve. In fact, since 1999, the technologies manufactured in Sudbury by Ionic and the expertise developed by its team of more than 150 people have been making mines and metal refineries on every inhabited continent safer and more productive.
In 2005, the company designed and manufactured the world’s first robotic copper stripping systems for use in refinery tankhouses as far away as South Korea, China, and Zambia.
Founded as Ionic Engineering by the late Steve Matusch, the company has grown into one of the most important manufacturers within Sudbury’s world renowned mining technology cluster. Matusch’s goal of developing and manufacturing technologies that helped clients achieve higher rates of productivity within a smaller footprint set the stage for international growth and expansion.
In 2005, the company designed and manufactured the world’s first robotic copper stripping systems for use in refinery tankhouses as far away as South Korea, China, and Zambia. At the same time, relationships built with local mining and refining companies like Inco (now Vale Canada) allowed Ionic to compete with much larger international companies in Sudbury and elsewhere in Canada.
Today, the multi-divisional company operates facilities in Sudbury and Cambridge. The Sudbury facility has been located in Lively since it outgrew its original facility in 2005. It houses five of the company’s divisions:
Ionic Mechatronics (website), which develops and manufactures automated mechatronic equipment used in material handling and processing at mines, refineries, and other heavy industry operations. This generally involves low volume and modular production of very large and heavy equipment that is designed to last more than 25 years;
Variant Mining Technologies (website), which manufactures ore and waste rock handling equipment for hard rock mining applications, and recently built and installed the world’s largest ore chute at Rio Tinto’s Oyu Tolgoi mine in Mongolia;
Desom (website), which develops ventilation systems for refineries and other heavy industry applications;
Synaptic Technologies (website), which develops Internet of Things (IoT) software and manufactures hardware (including IoT sensors) used in critical infrastructure; and
SafeBox (website), which manufactures automated de-energizing lockout systems.
The 25,000 square foot location in Lively has expanded on several occasions, including most recently in 2020 in response to high demand for Ionic’s products.
The automated equipment produced and installed by Ionic offers a solution to labour shortages, and also helps mining and refining companies improve productivity and safety...
Much of Ionic’s growth is closely related to broader trends in the global mining industry. While individual pieces of equipment are often highly customized, Ionic’s clients across the world are seeking solutions to similar challenges. Perhaps the most pressing are labour shortages and the strong demand to increase operational safety. Mining and refining companies are often located in remote regions, and despite high rates of compensation, struggle to attract and retain talented operators. The automated equipment produced and installed by Ionic offers a solution to labour shortages, and also helps mining and refining companies improve productivity and safety, especially during the initial phases of extraction and production.
At a time when the demand for minerals is expected to surge with the production of batteries for electric vehicles and other clean energy applications, automation becomes the most viable option to scale up production. In places like Africa, Latin America, and Asia, the demand for mining and refining automation products is booming alongside operations in and around Canada. These trends have kept Ionic busy with work over the past few years and the company is operating at capacity today.
Mining and refining companies are also increasingly concerned with health and safety. Like labour shortages, automation offers a solution to these challenges. Put simply, robots and other automation technologies keep operators away from the most dangerous areas of mine or refinery, without sacrificing productivity or quality.
While Ionic’s core business remains focused on mining and refining equipment, it is constantly developing new technologies and solutions for its clients.
The company’s Ionic Automation division is located in Cambridge, and serves the life sciences and automotive industries primarily. It doubled in size about five years ago. Ionic’s Black Rock Engineering division, which is led by current CEO Christina Visser and provides mechanical and electrical engineering services to mining and manufacturing clients, operates from an office in Sudbury’s South End neighbourhood. A systems design engineer with more than a decade of experience working for Inco, Visser joined Ionic in 2005 and has helped chart the growth of the company since Matusch, her husband, passed away in 2020.
The multi-divisional organization of Ionic provides the company with an important competitive advantage. While Ionic’s core business remains focused on mining and refining equipment, it is constantly developing new technologies and solutions for its clients. When one of those technologies demonstrates substantial growth, it is spun off into its own division. Ionic hires divisional managers with entrepreneurial backgrounds and a deep understanding of the technologies and markets associated with that division, which allows them to further develop those product lines. The broader company also benefits from the perspectives of divisional managers. This is especially important considering that industrial and mining automation lies at the intersection of mechanics, electronics, and software engineering.
Another advantage of the multi-divisional structure for Ionic is the way it allows the company to draw on from different pockets of knowledge stored in each of its divisions and then apply that knowledge elsewhere. For instance, the Ionic Automation group in Cambridge builds automation products for industries that have shorter equipment renewal cycles. They get more experience working with new technologies. The Ionic Mechatronics group in Sudbury can learn from their colleagues in Cambridge about these technologies and incorporate them into the products they develop.
The company recruits extensively from local mechatronics and robotics programs offered at Sudbury-based Cambrian College, Collège Boréal and Laurentian University, and at Sault College in Sault Ste. Marie.
In addition to its proximity to mines and one of the world’s most well-developed mining technology clusters, Ionic’s location in Sudbury offers a number of advantages not available elsewhere. The company recruits extensively from local mechatronics and robotics programs offered at Sudbury-based Cambrian College, Collège Boréal and Laurentian University, and at Sault College in Sault Ste. Marie. The company collaborates closely with NORCAT and with Cambrian R&D (the college’s applied research department), sometimes engaging them to aid with concepts, design, and fabrication work.
Ionic takes advantage of a number of government programs designed to support technology manufacturers and exporters. Many Ionic projects include an R&D component and are eligible for Scientific Research and Experimental Development (SR&ED) tax credits or the National Research Council of Canada Industrial Research Assistance Program (NRC IRAP) assistance. The company also receives support from Global Affairs Canada’s Trade Commissioner service and Export Development Canada (EDC). This, as Ionic Mechatronics’ Business Development Manager Ryan Catton noted, has been critical in helping the company de-risk business development activities in South Africa and Chile.
Ionic has also introduced a scholarship program in collaboration with Cambrian’s mechatronics program, in honour of Matusch.
Ionic’s management stresses the importance of being involved in the community and in the broader technology ecosystem. Matusch was a co-founder of Sudbury ROCKS!, a local running club that has hosted an annual marathon since 2005, with all proceeds going to the Northern Cancer Foundation. Visser has served on the Ontario Society of Professional Engineers’ (OSPE) board of directors, and is also the founding president of the Sudbury chapter of Women in Science and Engineering (WISE).
Ionic has also introduced a scholarship program in collaboration with Cambrian’s mechatronics program, in honour of Matusch. For these, and other initiatives, Ionic received a North Ontario Business Award in 2015, a Canadian Business Excellence Award in 2021, and named Cambrian College’s 2021 Employer Award of Distinction.
The latter award reflects the value that Ionic places on creativity and problem-solving, which lead to rewarding and solutions-oriented careers that allow local graduates to bring Sudbury-made technologies to mines and refineries across the world.
For more information about Ionic Technology Group, visit their website.
Published: September 12, 2023
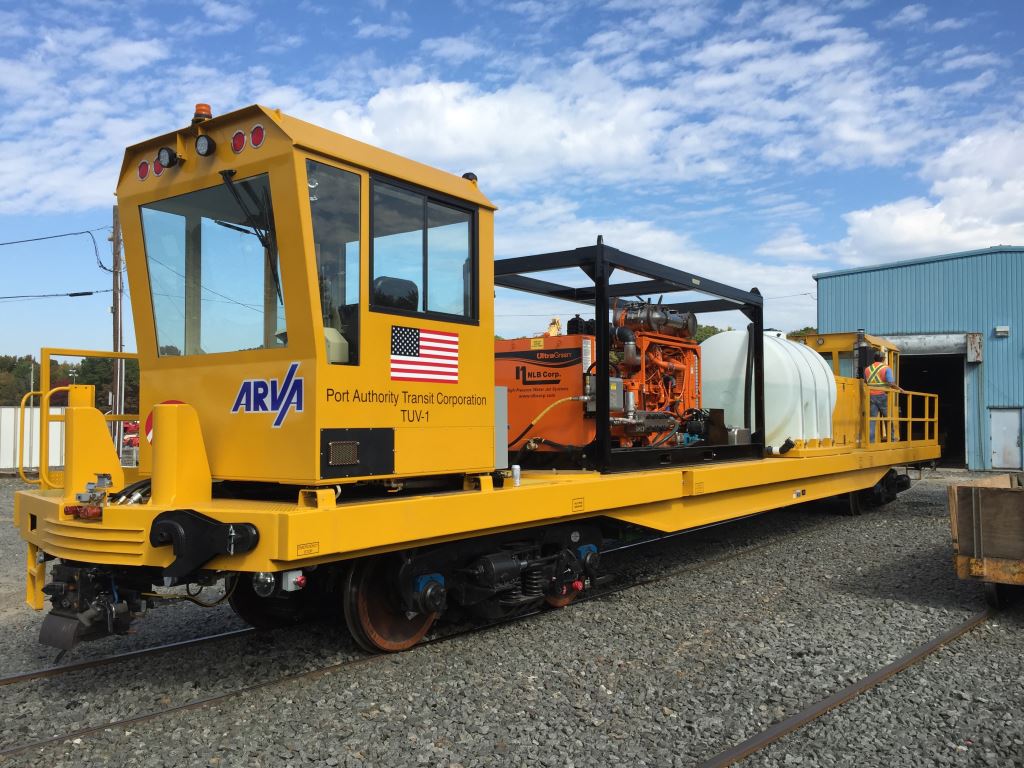
Arva Industries
Located in St. Thomas, Ontario, Arva Industries manufactures high-quality, durable equipment and vehicles that combined with its collaborative and team-oriented approach to customer relationships give the company a positive reputation across many industries.
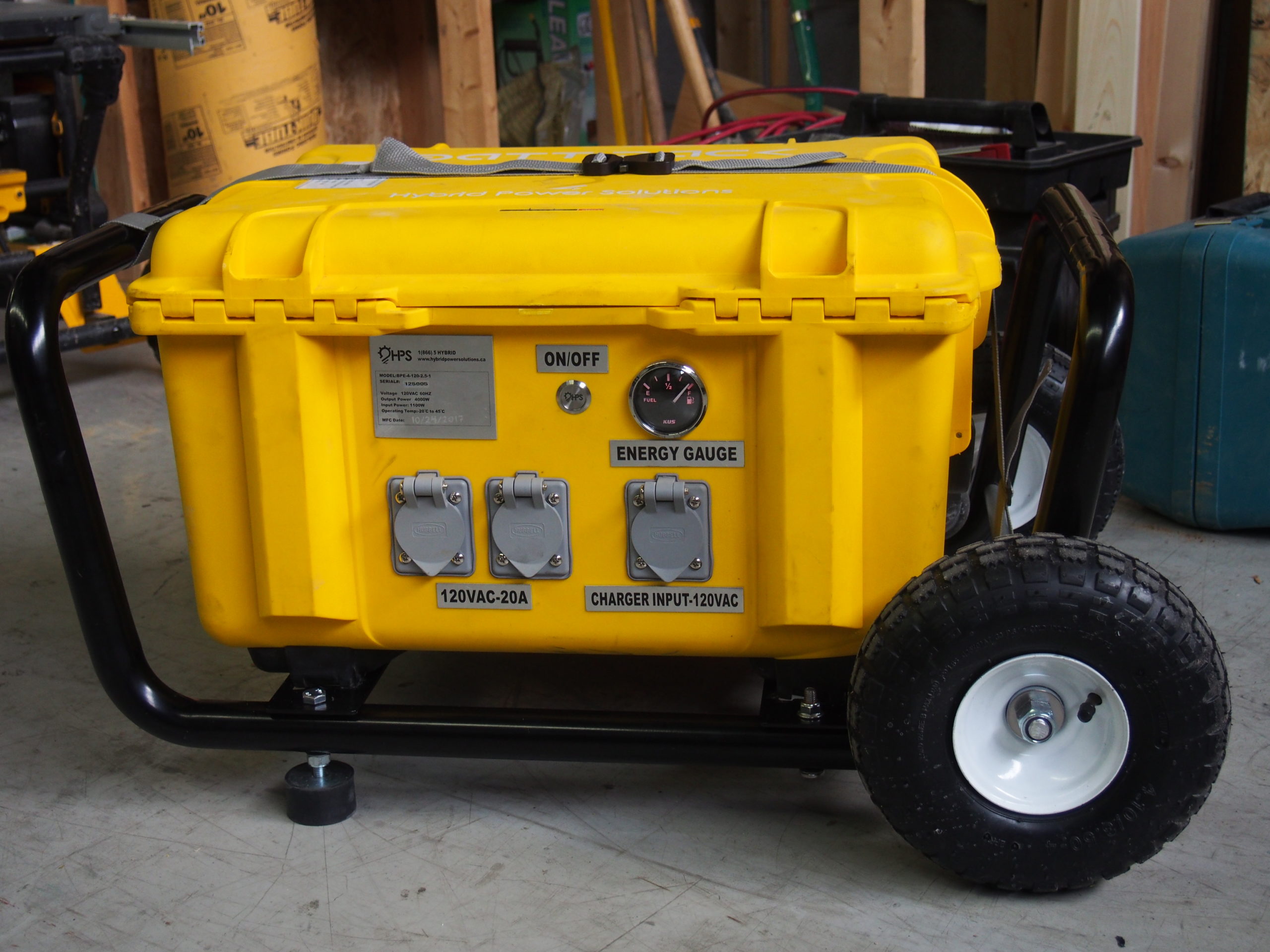
Hybrid Power Solutions
Hybrid Power Solutions produces portable battery systems and customized energy solutions for a variety of industrial markets.
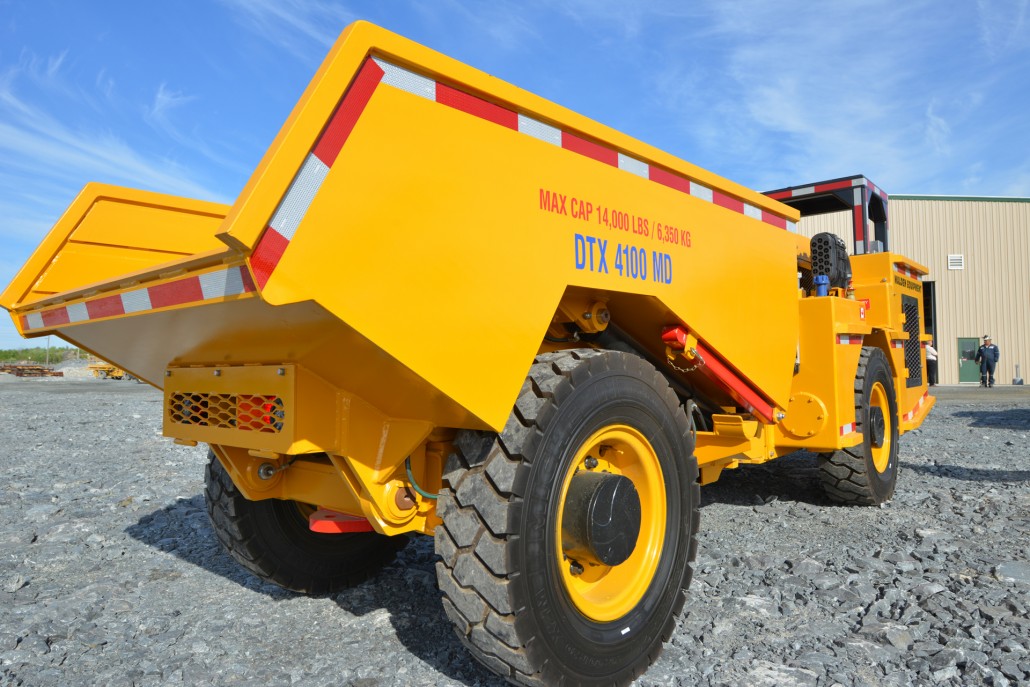
J&S Manufacturing
J&S Manufacturing is a mining equipment manufacturer, with in-house design capabilities that allow the firm to manufacture mobile equipment as well as technical custom equipment. The company’s motto is “Built to Perform”.
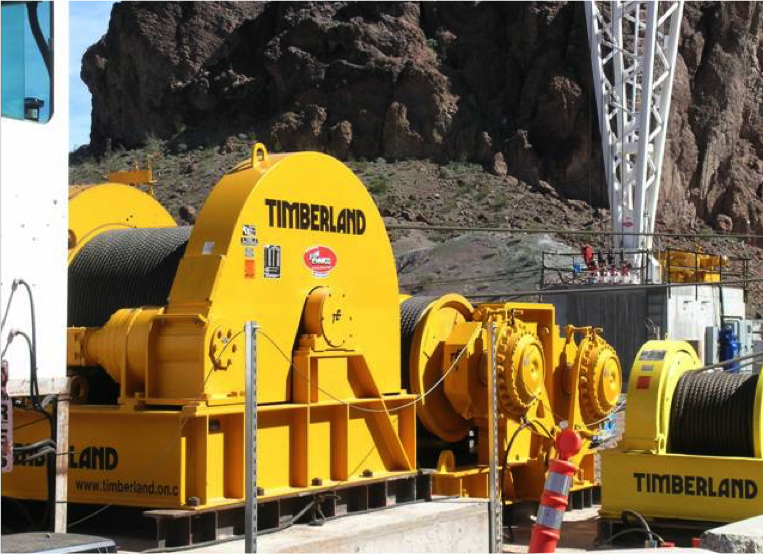
Timberland Equipment
Timberland Equipment is a global leader in the integrated design, manufacture and support of engineered winches, hoists, sheaves, derricks and tensioning equipment for the world’s most challenging infrastructure and capital equipment projects.
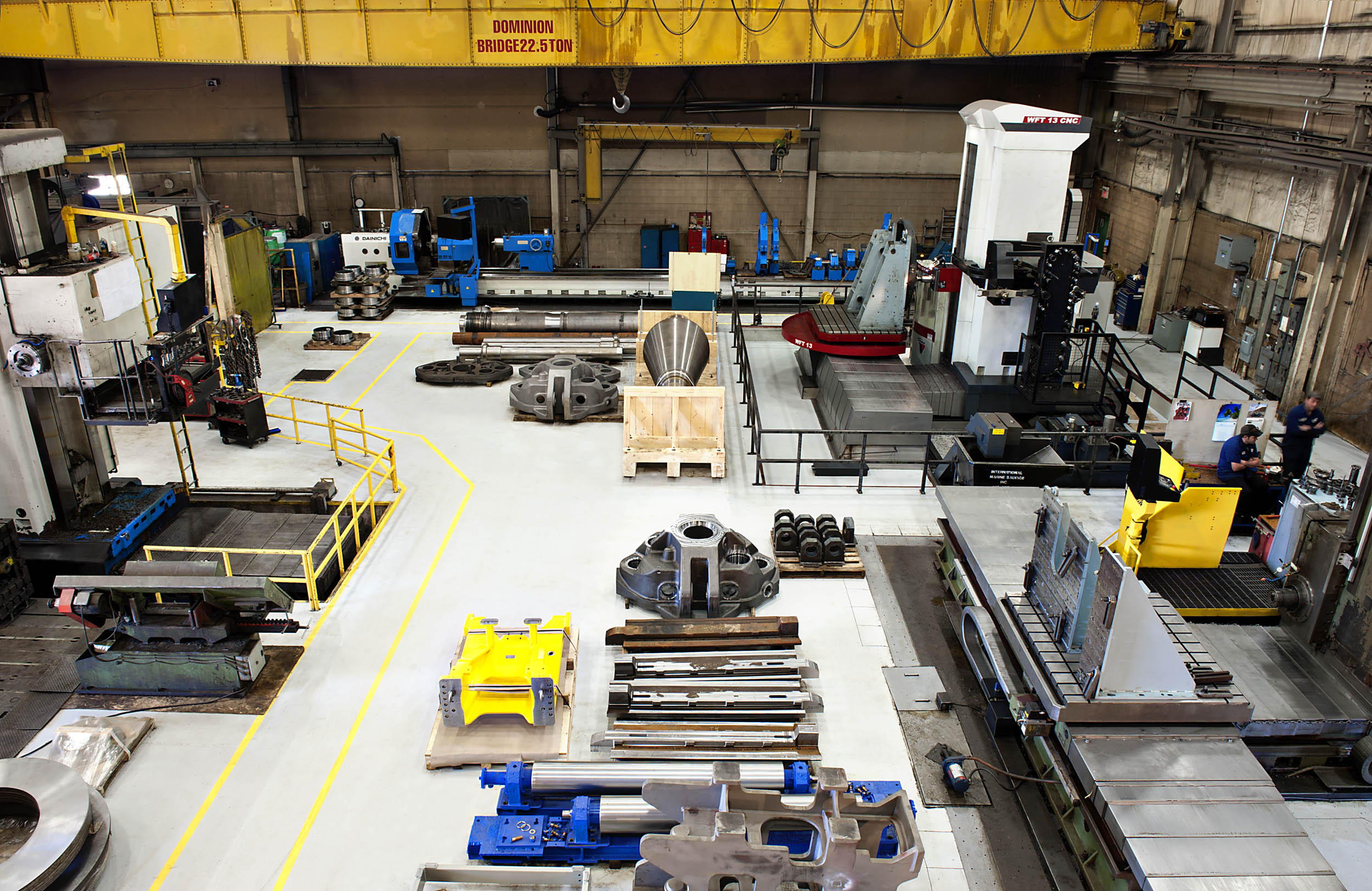
CMI Heavy Industries
CMI Heavy Industries is a leading provider of heavy fabricated, forged and cast machined components and assemblies.