-
Headquarters -
51 Centennial Road, Orangeville, ON L9W 3R1
-
Year established -
1988
-
NAICS -
326198 - All other plastic product manufacturing
-
Major expansions -
2006
-
Employees -
177
-
Exports -
US
-
Download -
e.Hofmann Plastics Inc.
Innovation and automation. Paul Kalia, chief executive officer at e.Hofmann Plastics Inc. (Hofmann Plastics), notes that these two ideals are the keys to running any successful manufacturing business, and the aims that drive his company’s strategy. The company is in what Kalia refers to as the “rigid packaging business”. It manufactures plastic buckets for industrial markets (such as the orange buckets seen at Home Depot) and plastic packaging for the food and beverage industry. However, Kalia does not see Hofmann Plastics as a plastics company; instead, he views it as a technology company that is constantly innovating and looking for new ways to solve problems.
Innovation and automation. Paul Kalia, chief executive officer at e.Hofmann Plastics Inc. (Hofmann Plastics), notes that these two ideals are the keys to running any successful manufacturing business, and the aims that drive his company’s strategy. The company is in what Kalia refers to as the “rigid packaging business”. It manufactures plastic buckets for industrial markets (such as the orange buckets seen at Home Depot) and plastic packaging for the food and beverage industry. However, Kalia does not see Hofmann Plastics as a plastics company; instead, he views it as a technology company that is constantly innovating and looking for new ways to solve problems.
Hofmann Plastics began as an Austrian company located in Brampton, Ontario in the early 1980s. Kalia came across the opportunity to purchase it in 1988, when sales were low and it was struggling to stay afloat. He and three other partners joined together to buy Hofmann Plastics, with the hope of turning things around. After several years of familiarizing themselves with the business and shaping it into what Kalia envisioned it could be, sales began to take off. The company roughly doubled between 2000 and 2004. In 2006, Hofmann Plastics relocated to its current Orangeville location to accommodate this booming growth.
However, in 2008, the global recession caused many of Hofmann Plastics’ largest customers to disappear, putting significant strain on the business. Kalia bought out his partners, taking sole ownership of the company, and proceeded to weather the storm by doubling down on his belief in innovation and automation.
Today, Hofmann Plastics’ 175,000-square-foot state-of-the-art manufacturing facility houses the most advanced injection moulding and thermoforming machines available.
Since 2008, Hofmann Plastics has continued with (and increased) this commitment to innovation and automation. The company believes that innovation helps create new products and satisfy market desires, while automation helps meet the capacity demands of its large customer base. This two-pronged strategy has caused sales to grow 2.5 times since 2009, and the number of employees to grow to 177. Today, Hofmann Plastics’ 175,000-square-foot state-of-the-art manufacturing facility houses the most advanced injection moulding and thermoforming machines available. Employees are constantly inventing new products, improving the manufacturing process, and leveraging the technology available to them to tackle new challenges.
Hoffman Plastics’ approach to innovation is one any company can follow, regardless of size or industry. Employees are asked to go out and find a problem and think of some ways they can fix it. This problem can be something as small as finding a better way to clean a remote section of the plant floor, or something as big as inventing an entirely new product. “Innovation has no one place” Kalia notes, meaning that innovation begins when an employee looks at any aspect of the business and considers how it can be improved.
“Innovation has no one place” Kalia notes, meaning that innovation begins when an employee looks at any aspect of the business and considers how it can be improved.
Excelling in innovation is key for Hofmann Plastics because today’s plastics industry puts increasing value on manufacturers that are able to come up with new, environmentally friendly solutions. The company has always focused on making the world a better place, and now it is looking at producing new products that are compostable as well as high-quality, cost-effective, and compatible with existing machinery. Hofmann Plastics sees this as an exciting challenge that will require extensive research and development and innovation.
Hofmann Plastics’ reputation for innovation is fueled in large part by its mix of old and new employees. Older employees, says Kalia, are great for the company because they have years of knowledge and experience. At the same time, complementing these employees with bright, young minds coming fresh out of school fosters an environment of excitement and advancement. Hofmann Plastics specifically seeks to hire engineers and technicians, because their skillsets are best suited for leveraging the company’s advanced technology and inventing new products.
The second branch of Hofmann Plastics’ strategy, automation, enables the company to fulfill the product volume demands of its customers. Being a world leader in the plastics industry not only requires a company to produce innovative products, but to supply them on a large scale as well. Hofmann Plastics’ chief technology officer, the plant manager, coordinates the logistics of the new technology to ensure everything is operating efficiently and effectively.
The other significant benefit of automation is that it improves the day-to-day experience of employees on the plant floor. The company’s aim is to give machines the tasks that require substantial manual human effort, thus freeing up employees’ energy and time to focus on tasks more suited to human cognition (like innovation).
It is important to note that automation at Hofmann Plastics does not spur layoffs; rather, it improves the employee experience. Kalia is thoroughly tired of hearing Ontario manufacturers complain about labour costs because he thinks it is wrong to look at employees as simply a number on the bottom line. Instead, he argues, employees should be viewed as partners, and wages paid to them are better thought of as a “thank you” for contributing to the company’s success. Automation allows Hofmann Plastics to take this approach by making employees more effective while simultaneously improving their overall job experience.
Hofmann Plastics ensures it has the capital to follow its dual goals of innovation and automation, reinvesting 15–20 per cent of revenue back into the company each year. Additionally, the company plans to increase the dollar value of this reinvestment over the next three years.
The most pressing challenge for Hofmann Plastics is attracting qualified workers to join the company, particularly skilled trades graduates and engineers. The company is addressing this gap by trying to disseminate the message that the company is a technology company, not a plastics company, and one with endless opportunities for smart, creative people to begin new projects. In fact, Kalia likes to think of the company as a start-up with a cash flow. This is because new products are constantly being developed and each initiative brings its own set of risks, challenges, and rewards, just like those taken on by the tech start-ups found in Waterloo or Silicon Valley.
A big part of the company’s strategy moving forward is the shift towards sustainable packaging. This is a logical step for the firm because it intertwines the company’s two guideposts: innovation and automation. Fortunately, because of its strategic aims, Hofmann is already on the right path. Most recently, they invested in advanced thermoforming technologies capable of processing Polypropylene (PP) based rigid K-Cup’s & meat trays. PP based products provide a safer alternative to Polystyrene because they do not produce Benzene during the recycling process.
Although producing more recyclable packaging is a step in the right direction, the company’s R&D team has worked alongside a number of Canadian Universities to produce prototypes for biodegradable bioplastic coffee pods & meat trays. The aim is to bring these to market at a price similar to plastic based alternatives. In addition, the company is looking to offer products that incorporate bio-digestive resin, which uses enzymes to digest the plastic into sustainable by-products. Their goal is to offer these in 2019, and help be an industry leader in sustainable packaging.
These initiatives are just a few examples of the exciting developments underway at Hofmann Plastics. With Kalia’s leadership and the company’s continued commitment to innovation and automation, the firm will undoubtedly remain one of Ontario’s top manufacturers in today’s competitive global environment.
For more information about e.Hofmann Plastics Inc., visit their website.
Published: November 6, 2018
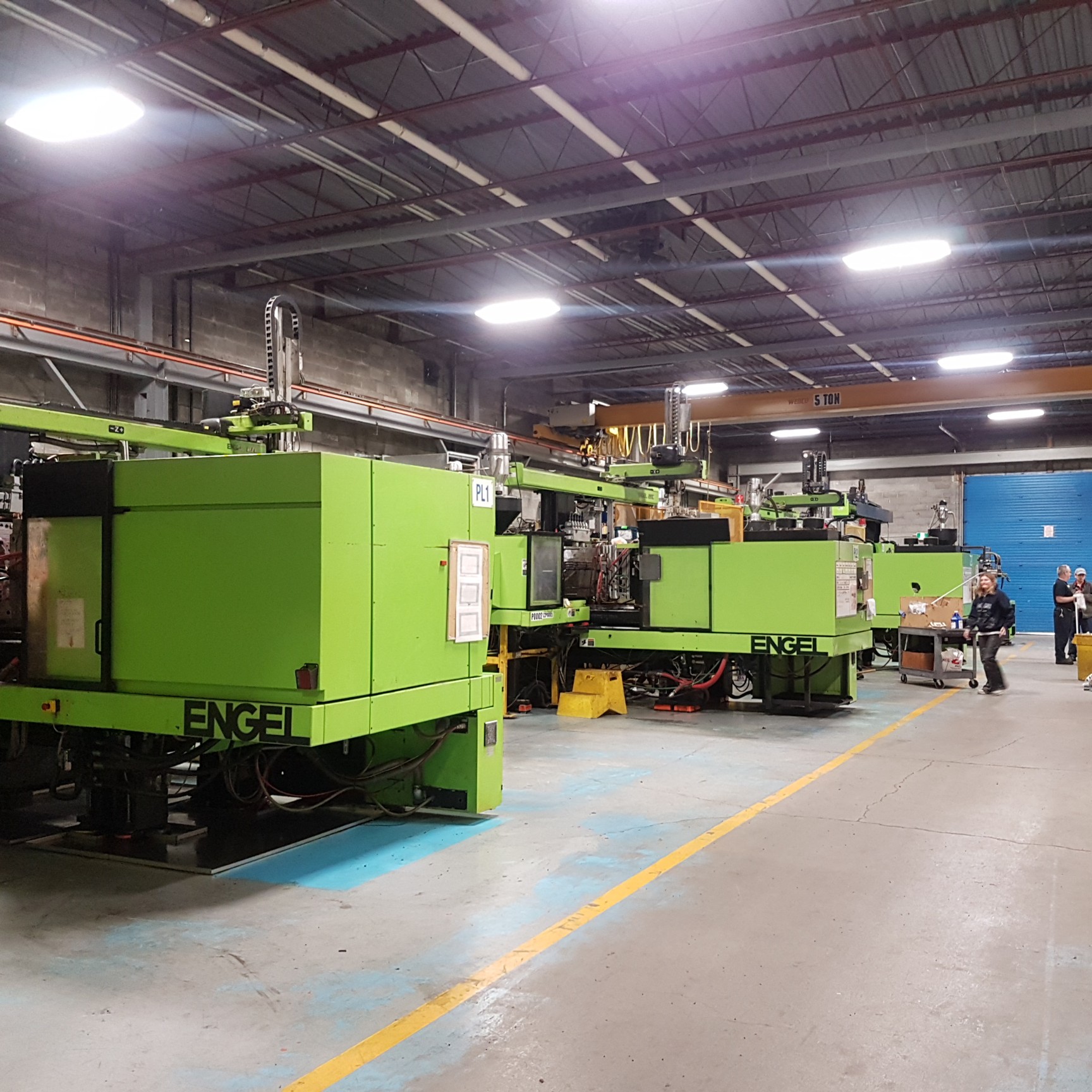
WEGU Manufacturing Inc.
WEGU Inc. is a multi-international manufacturer of molded rubber and plastic products. Product design assistance, engineering, tooling development, prototyping, testing and manufacturing, and materials analysis, are all offered in house. WEGU Inc. prides itself on the ability to consistently meet all of their client’s physical and chemical requirements for product durability, flexibility, noise and vibration mitigation, and abrasion resistance.
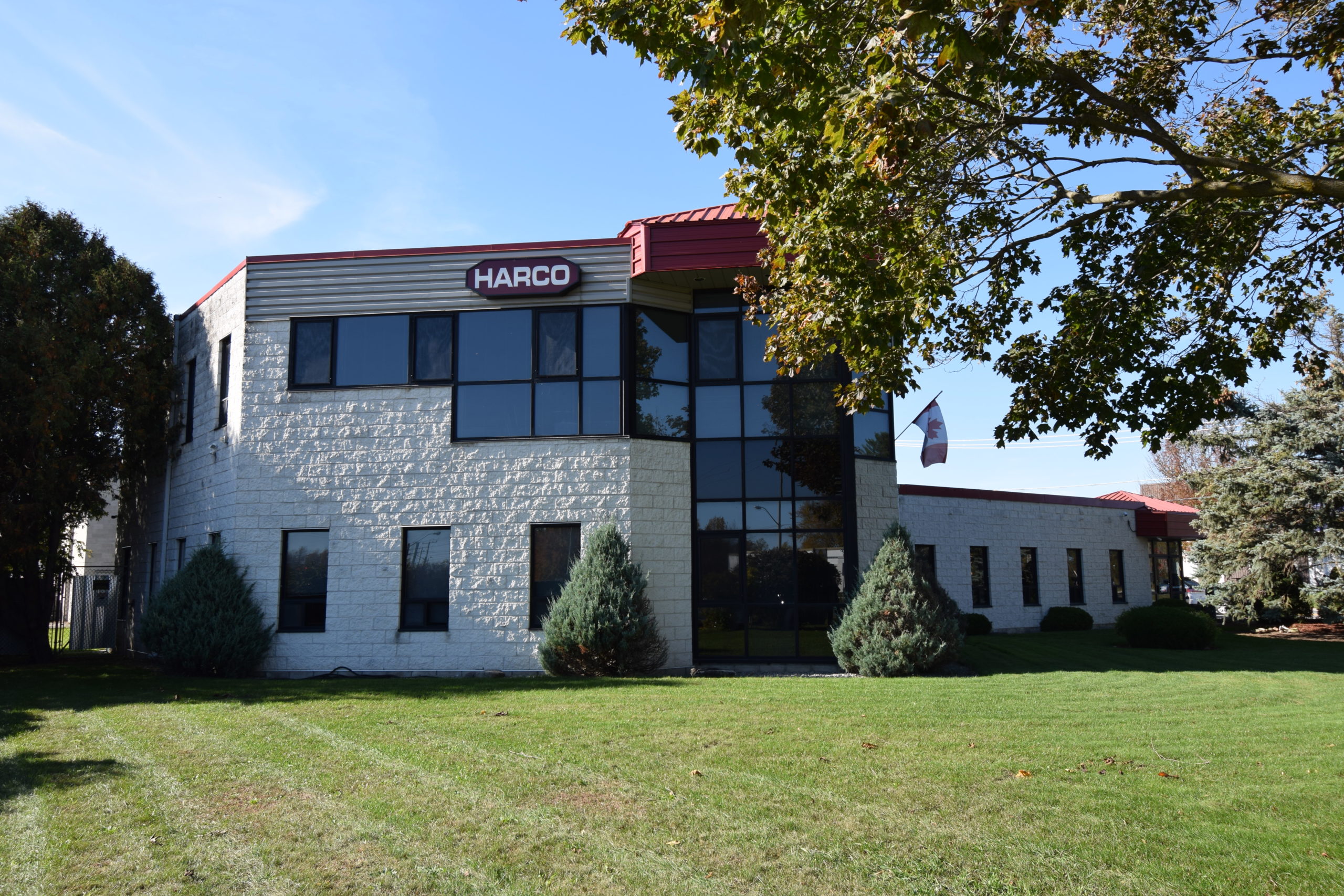
Harco Enterprises Limited
Harco is fourth-generation family business which operates two distinct divisions: Plastic Injection Molding and Process & Supply, which distributes sanitary processing equipment and components. The firm has a flexible product line, and is always looking for new market opportunities to take advantage of.
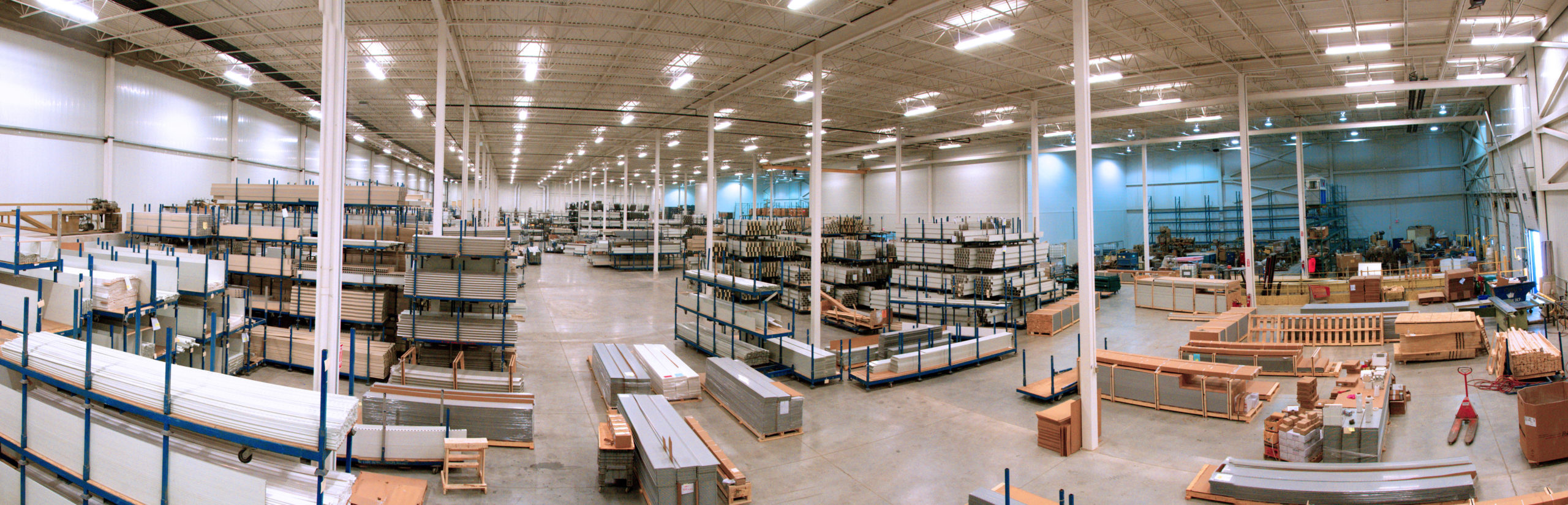
Nuform Building Technologies
Nuform Building Technologies is North America’s leading manufacturer of finished concrete forming systems, providing services of estimating, design, technical assistance, transportation and logistics, and onsite field training.
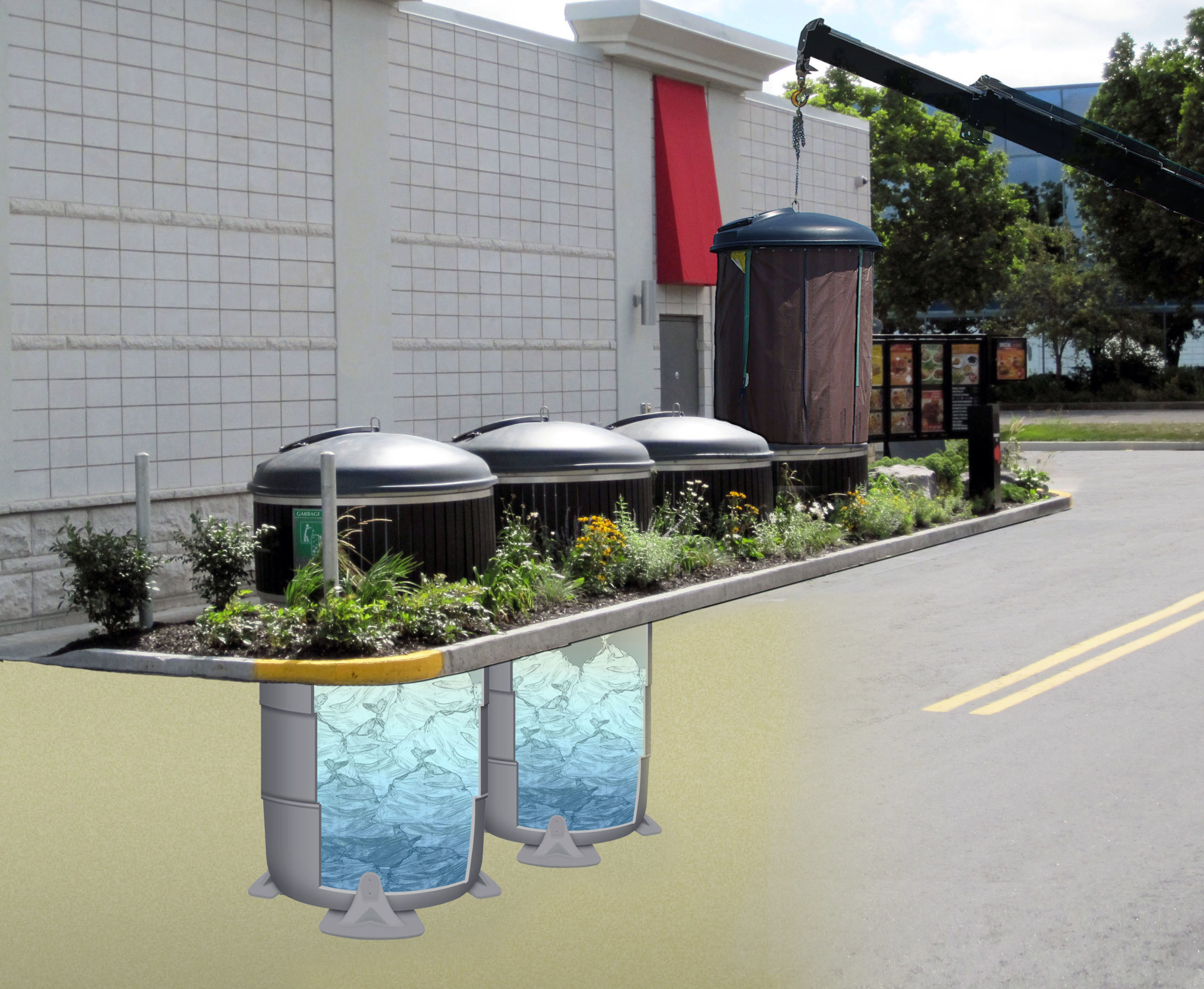
Molok North America
Molok is a new generation designer and manufacturer of the original semi-underground waste containment systems.
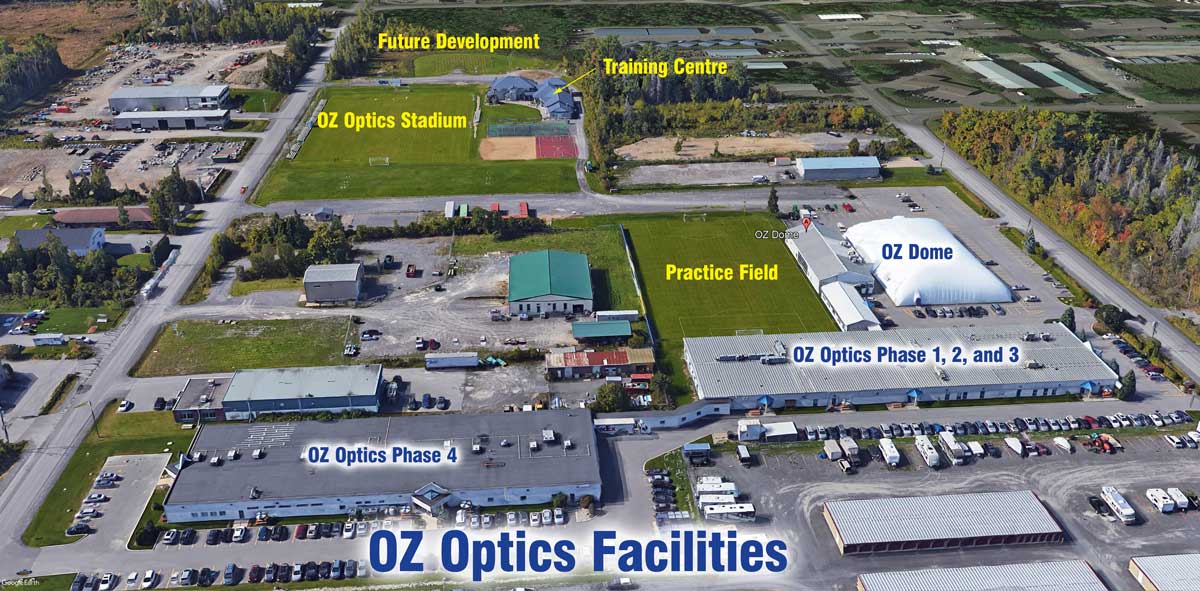
OZ Optics Ltd.
OZ Optics designs and manufactures advanced fiber optic components and test equipment for various fiber optic markets. The company implements rigorous quality standards to achieve its goal of providing all customers with a competitive advantage, and has become a leading worldwide supplier of optic products.