-
Headquarters -
222 Snidercroft Rd. Suite 222, Concord ON L4K 2K1
-
Year established -
2001
-
NAICS -
334512 - Measuring, medical and controlling devices manufacturing
-
Major expansions -
-
Employees -
49
-
Exports -
China, Romania
-
Download -
Sartrex Power Control Systems Inc.
Sartrex Power Control Systems is a scientific instrumentation company that designs and manufactures custom safety critical equipment, primarily for the nuclear industry
This industry depends on highly reliable, fail-safe equipment that is designed to withstand extreme environmental and operating conditions for over 30 years. Sartrex responds by nurturing a loyal workforce that operates under a “no room for error” philosophy. The company’s reputation depends on its ability to ensure its customers’ safe operations, and it achieves this by operating in a zero-defect environment.
The 25 employees who were there in 2001 are still with Sartrex today.
In addition to nuclear, Sartrex supplies custom-designed control and safety instrumentation for military and security applications, and scientific laboratories. The company is located in Vaughan, in a 45,000 square foot manufacturing facility employing 55 people. There has been virtually no turnover since the company was founded in 2001. The 25 employees who were there in 2001 are still with Sartrex today.
The company name ‘Sartrex’ is a combination of the founder’s name, ‘Sarkar’, and ‘Scintrex’, its corporate predecessor. Jay Sarkar, president, chief executive officer and board chair of Sartrex, began working for Scintrex, an instrumentation manufacturer, in 1977. He started out as a junior engineer, and eventually earned a position of Senior VP of Sales and Marketing. Under his leadership, the nuclear and military division of Scintrex became its most profitable business unit. When Scintrex was acquired by another company and broken up, Sarkar bought the nuclear and military division, fulfilling his lifelong ambition of being an entrepreneur, a dream of his since immigrating from India.
All design, manufacturing, testing, and qualification activities are performed in Vaughan, Ontario, Canada.
Sartrex’s core business is designing and manufacturing safety shutdown solutions that measure very low signal (picoamp range), a refined measure of electrical current to help control and monitor the reactor performance. If these solutions do not operate as expected the power plant will be shut down. Most importantly, these custom-made front-line defense systems that are designed to meet very specific operating requirements are used to initiate a plant shutdown sequence in the event of a threat to the public during an emergency. Shawn Sarkar, the founder’s son and executive vice president, describes this as “a great incentive to deliver a perfect product.”
Sartrex currently has over 4000 custom made instrumentation and control systems installed in nuclear power plants around the world. All design, manufacturing, testing, and qualification activities are performed in Vaughan, Ontario, Canada.
One example of its use is the Sartrex-designed instrumentation deployed at the CANDU nuclear reactor sites in Canada. Various indicating meters and current alarm units are installed on specialized equipment, including ion chamber amplifiers, signal isolators, conductivity transmitters, in-core flux detectors, failed fuel detection systems, tritium monitors, control panels, trip test amplifiers, temperature transmitted etc. All custom safety critical amplifiers use best practice design, manufacturing, and procurement techniques to ensure they meet the most demanding and meticulous manufacturing practices in the world.
To deliver the perfect product, Sartrex relies on both people and process.
To deliver the perfect product, Sartrex relies on both people and process. Employees are a mix of engineers, scientists, technologists, and electronic assemblers, all of whom are continuously trained and retrained on critical practices. With exceptionally low turnover, the company can invest in expanding the capability of the existing workforce instead of training new employees, a practice that helps to reduce costs. As an immigrant himself, Jay Sarkar recruited many of the long-standing employees from Ontario’s Bengali-Canadian community. The company supplements technical training with soft skills training to help employees adapt to cultural differences that they might encounter in the Canadian business environment.
In addition to developing best practices over 40 years in this space, the manufacturing processes for this type of equipment are guided by the Institute of Printed Circuits (IPC) industry standards that ensure quality in the electronics. The company holds ISO 9001:2015, CSA-N299 and ASME NQA-1 certifications for the development and manufacturing of scientific instruments for the power generation and instrument control markets. It invests heavily in R & D and has introduced innovations including an autonomous drone to work in a no-GPS environment. The company uses prototyping and design for manufacturing techniques when helping its customers move from the conceptual design phase to tangible, production ready product.
The majority of Sartrex’s customers are power generation companies. Across Canada, these include Ontario Power Generation, Bruce Power, Hydro-Québec, and NB Power. It also serves the nuclear industry in South Korea, China, Romania, and Argentina. It supplies each customer with a different mix of instrumentation and control solutions, all with a safety related focus. One unique Sartrex-built monitoring system is a custom designed radiation detection system that has been installed at the Canadian Forces Bases in Halifax and Esquimalt, and at the Maritime Engineering Test Range in Nanoose Harbour, British Columbia. The system measures gamma radiation from visiting nuclear powered vessels. If radiation is detected at above safe levels, the system triggers an emergency response process with National Defence Headquarters.
One unique Sartrex-built monitoring system is a custom designed radiation detection system that has been installed at the Canadian Forces Bases in Halifax and Esquimalt, and at the Maritime Engineering Test Range in Nanoose Harbour, British Columbia.
In addition to nuclear, Sartrex is expanding its footprint in the medical and aerospace industries, which also demand zero-defect products. Both industries require engineering solutions that conform to robust quality and design standards. Aerospace is a lower volume industry; however, the design and manufacturing techniques must withstand extreme environmental and operating conditions, coupled with precise accuracy and decades-long reliability. Shawn Sarkar describes this as “a nice pivot for us, as we are a premier supplier of safety critical instrumentation for the nuclear industry whose design and manufacturing capability requirements are equally demanding.” The Quality Assurance programs that are applied to the nuclear, aerospace, and military industries are very similar, so obtaining the proper certifications is a seamless process for the company.
However, the company’s current focus is to continue supporting CANDU Nuclear Power Plant refurbishment strategies. All three Canadian Nuclear Providers are extending the life of the reactor another 30-40 years, which requires replacing legacy systems that are coming to end of life. This is challenging, as many components are obsolete, or the original manufacturers are no longer in business or no longer supporting the product. Sartrex’s agile production force, with an expertise in low volume and high mix, coupled with their 40-year operational experience uniquely positions them to add considerable value to this major undertaking.
Given there are pros and cons of both modular and traditional projects, Sartrex is staying close to the global engineering effort to bring SMR technology to the market, as it represents yet another opportunity for a company that specializes in enabling the safe operation of critical technology.
Looking to the future, Sartrex is conscious of the emerging shift from traditional nuclear to small modular reactors (SMRs). However, the company is confident that the traditional nuclear industry will continue to represent an important market for many years. There are over 100 new planned nuclear builds around the world, representing both traditional and modular design. At the same time, the industry is pushing to extend the life of existing operating licenses, doubling the life of plants that were originally intended to last 25 to 40 years. This is viewed as a cost-effective way to maintain a country’s electricity capacity without investing in developing replacement capacity. Bruce Power, the largest nuclear fleet in the world, is currently refurbishing its eight reactors to extend its life to 2064. NB Power and Ontario Power Generation have taken a similar approach.
In addition to refurbishing to bring dormant reactors back into service, the United States, Switzerland, Spain, Finland, and Sweden are increasing their nuclear generating capacity by uprating their functioning reactors; increasing their generation capacity rather than replacing it with newer technology. While refurbishing and uprating are being used to extend and expand the useful life of existing reactors, Sartrex acknowledges that SMRs will continue to grow in dominance in the nuclear power generation space over the next 15 years. Given there are pros and cons of both modular and traditional projects, Sartrex is staying close to the global engineering effort to bring SMR technology to the market, as it represents yet another opportunity for a company that specializes in enabling the safe operation of critical technology.
For more information about Sartrex Power Control Systems Inc., visit their website.
Published: October 21, 2021
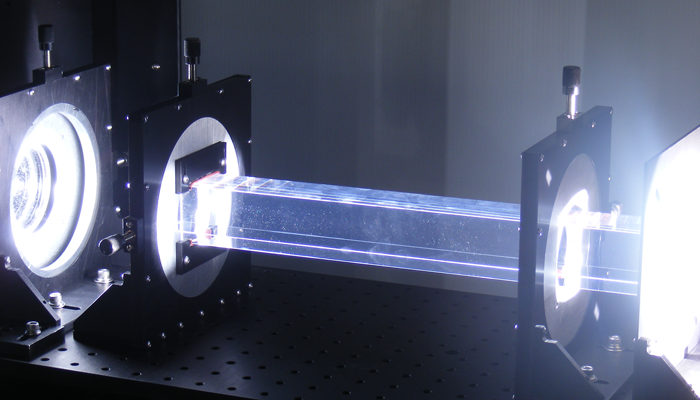
Sciencetech
Sciencetech designs and manufactures optical spectroscopic instruments, which are utilized across a wide range of industries and applications.
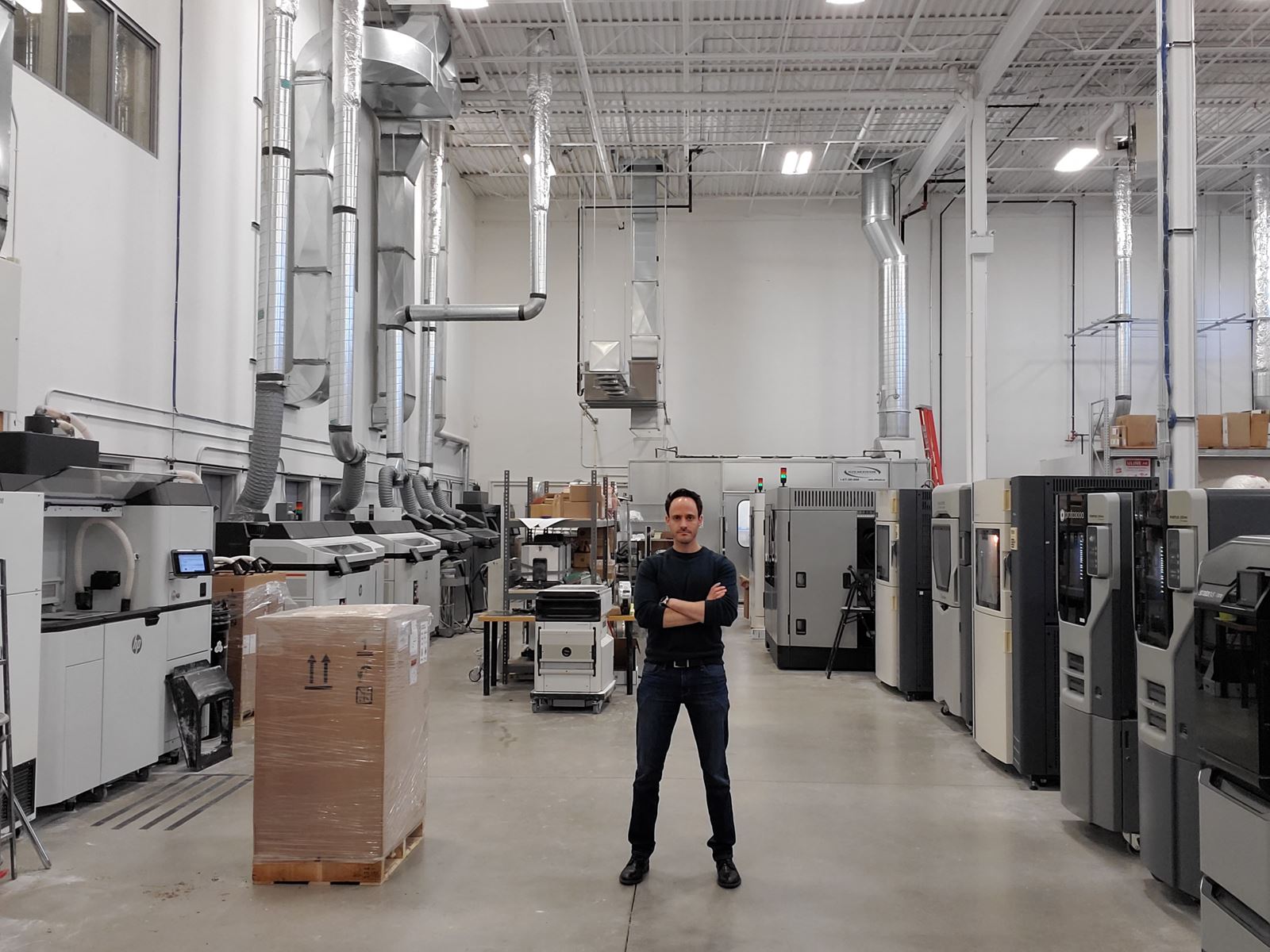
Proto3000
Based in Vaughan, Proto3000’s design, additive manufacturing, and metrology technologies help customers solve complex engineering and manufacturing challenges, resulting in shorter cycle times, more flexible supply chains, faster prototyping and more efficient production.
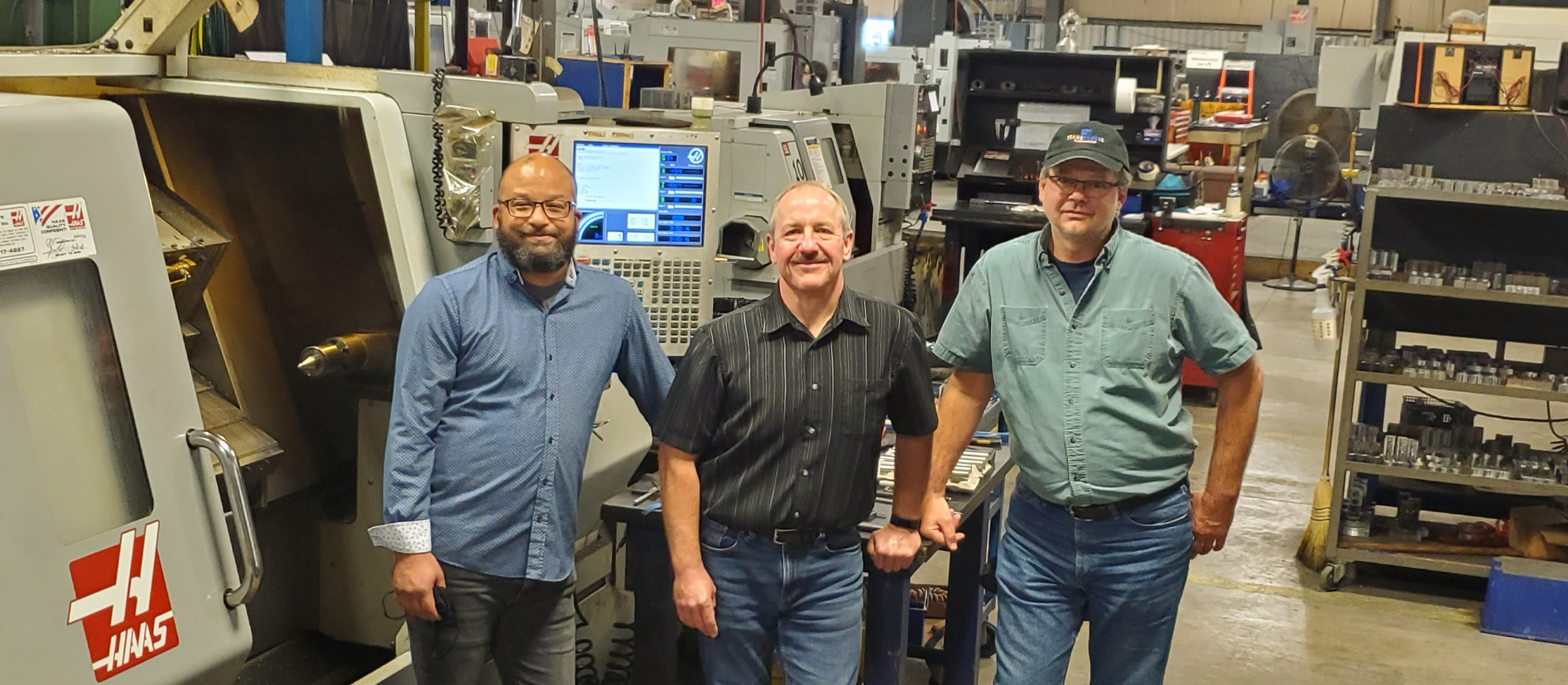
Nuformex Precision Manufacturing
Innovation, customer service, and problem-solving have helped make Nuformex Precision Manufacturing the success story it is today