-
Headquarters -
75 Tiverton Court, Markham, Ontario, L3R 4M8
-
Year established -
2006
-
NAICS -
334512 - Measuring, medical and controlling devices manufacturing
-
Major expansions -
N/A
-
Employees -
110
-
Exports -
US, Mexico, Asia-Pacific, EU
-
Download -
Bluewrist Robot & Vision Solutions
Bluewrist Robot & Vision Solutions designs and develops innovative industrial automation solutions in the fields of robot guidance and 3D machine vision.
Located in Markham, Ontario, Bluewrist Robot & Vision Solutions (Bluewrist) designs and develops innovative industrial automation solutions in the fields of robotics and machine vision. Every product at Bluewrist is created with the intention of increasing manufacturing efficiency and reducing operating costs and downstream defects for its customers. The firm’s intelligent software enables users to improve product quality by monitoring complex manufacturing processes via 100% inline inspection and statistical controls without hindering the speed of production. By contributing to the advancement of automation and quality control in its customers’ facilities, Bluewrist positively affects their production efficiency and product quality. Thanks to its leading-edge technology, competitive pricing, and highly effective customer support, Bluewrist has become a recognized leader in the delivery of flexible vision systems.
The founder of Bluewrist, Najah Ayadi, established the company in 2006, but the idea behind Bluewrist came to him much earlier. Prior to starting his own company, Ayadi worked at a plant that utilized automation technology and data analytics. He witnessed first-hand the issues that occur when open communication is lacking across all operating areas in a facility, and the limitations of using 2D vision systems for quality inspection. Ayadi’s experience in the automation industry and technical knowledge of robotic equipment gave him the appropriate skill set to successfully establish a company that would add value to manufacturers across various industries. Bluewrist has moved locations within Markham four times to accommodate its increasing domestic workforce, which has tripled over the last three years because of its rapid sales growth.
Bluewrist has developed four software products, each of which adds a different element to its customers’ operations: comXtream, SPCWorks, KinOptim, and ScanXtream. comXtream is an automation and communication engine that allows for data exchange among industrial devices like robot controllers, sensors, programmable logic controllers, and third-party software. ScanXtream is a metrology-grade 3D point cloud processing and viewing software that automatically analyzes point cloud data and compares it to a known model (typically a computer-aided design model), with the ability to extract features and compare surface dimensional variances. The main benefit of using 3D scanning is the availability of depth and volume information, which leads to more precise and accurate quality inspections. SPCWorks offers statistical data control through its instant collection of inspection data from inline and offline measurement systems, generating a variety of statistical reports for real-time quality control. KinOptim provides all-in-one, six-axis robot calibration that results in volumetric accuracy improvement, temperature compensation, and offline programming compensation. All of Bluewrist’s software is open source, which allows customers to integrate either custom hardware or standard off-the-shelf equipment into their own facilities.
The majority of Bluewrist’s customers operate in the automotive industry, mainly because firms in this field are usually the first to implement cutting-edge automation technologies. However, Bluewrist has recently begun expanding into non-automotive sectors as more industries become aware of the efficiency improvements that automation can bring.
Marketing and Communications Manager, Jason Niu, states, "Trade shows are still the company’s best marketing tool because there is no true substitute for face-to-face meetings in which potential clients can observe Bluewrist technology firsthand."
At the same time, the firm attracts some new customers by publishing stories on its website about unique applications of its technology, informing firms of the possibilities that Bluewrist products offer. Customers value Bluewrist’s products because they increase productivity through robotic automation and reduce the risk of passing defective parts downstream, which lowers overall costs. Rather than sampling parts for quality inspection, Bluewrist offers 100 percent inline inspection, meaning that each and every manufactured part is inspected. Moreover, all projects undergo comprehensive feasibility studies that are conducted at Bluewrist’s onsite innovation lab to ensure that they meet the firm’s quality standards prior to delivery. Bluewrist’s customers realize that producing a defective part and addressing the issue at a later date is significantly more expensive than identifying and resolving the issue immediately.
Although the majority of Bluewrist’s customers have already purchased hardware, the company has the internal expertise required to design and manufacture its own fixtures when customers request an in-house turnkey solution. Bluewrist’s domestic and international sales have benefited greatly from the global shift toward automation, as highly repetitive tasks become automated and employees are given more analytical jobs. The firm currently exports approximately 60 percent of its products, primarily to United States, Mexico and China. The scalability of Bluewrist’s products is what differentiates the firm from competitors in the automation industry. Bluewrist can offer solutions that utilize up to 30 plus cameras because of its scalable software, along with its expertise in perfecting the timing, path planning and coordination of each camera to minimize interference (e.g., if two cameras shine a laser on a product at the same time, one laser will distort the image being taken by the other camera). Most competitors are more proprietary and can only offer a fully integrated system if the customer purchases both hardware and software from them, making it too costly and too technically challenging to scale up operations as drastically as Bluewrist can.
Bluewrist employs approximately 100 individuals, with 60 working at the Markham facility and the remaining 40 stationed at facilities in China, Mexico, and the United States. These international locations were established to provide customers with accessible product installation assistance and troubleshooting customer service. The majority of employees hold various engineering degrees (e.g., mechanical, software, and electrical). Although the company has experienced rapid growth, Bluewrist has little difficulty recruiting talent. When hiring, managers emphasize how exciting it is to work at a high-growth company with a family-oriented work environment. Bluewrist also boasts a high retention rate, primarily because employees enjoy being consistently exposed to different manufacturers, products, and ideas. Rather than working on the same project every day, employees constantly face new challenges and are presented with countless opportunities to create solutions for cutting-edge problems.
Markham’s proximity to the U.S. automotive hub in Michigan is a strong advantage for Bluewrist, as it enables the firm to offer exceptional onsite customer support to its manufacturing clients across the border. In addition, Markham provides excellent access to both domestic and international talent from nearby universities. The firm has established partnerships with educational institutions such as Ontario Tech University and Queen’s University for collaborative research projects. Recognizing the importance of research and development (R&D), Bluewrist has intentions to become involved with the Ontario-based Next Generation Manufacturing Supercluster (NGen) endeavour. Prior research initiatives conducted by Bluewrist include collaboration with the Natural Sciences and Engineering Research Council of Canada, and participation in the Automotive Supplier Innovation Program, which saw Bluewrist receive $820,000 from the federal government in 2016. The company is also a member of the Robotic Industries Association, which gives it access to additional resources and a larger local network.
Bluewrist does not face any direct challenges at present, but the firm is constantly working to create a better algorithm that will provide customers with more accurate data within a smaller time frame, even though its current products already yield measurements with less than 0.01 mm of error. However, in the data collection and automation industry, the sky is the limit, and Bluewrist plans to focus its future R&D projects on new processes that can be utilized to detect product defects, such as machine learning, deep learning, or artificial intelligence. This R&D will have significant implications for quality inspections on welding and assembly seams because no two seams are ever the same. Bluewrist’s R&D team believe that by finding new algorithms and processes for the firm’s software, they can revolutionize the industry by improving upon the current best practice for defect detection, which is to compare a scanned product image with the original computer-aided design model. This drive to innovate and improve existing technology will help Bluewrist solidify its reputation as a global leader in intelligent automation systems.
For more information about Bluewrist Robot & Vision Solutions, visit their website.
Published: March 26, 2019
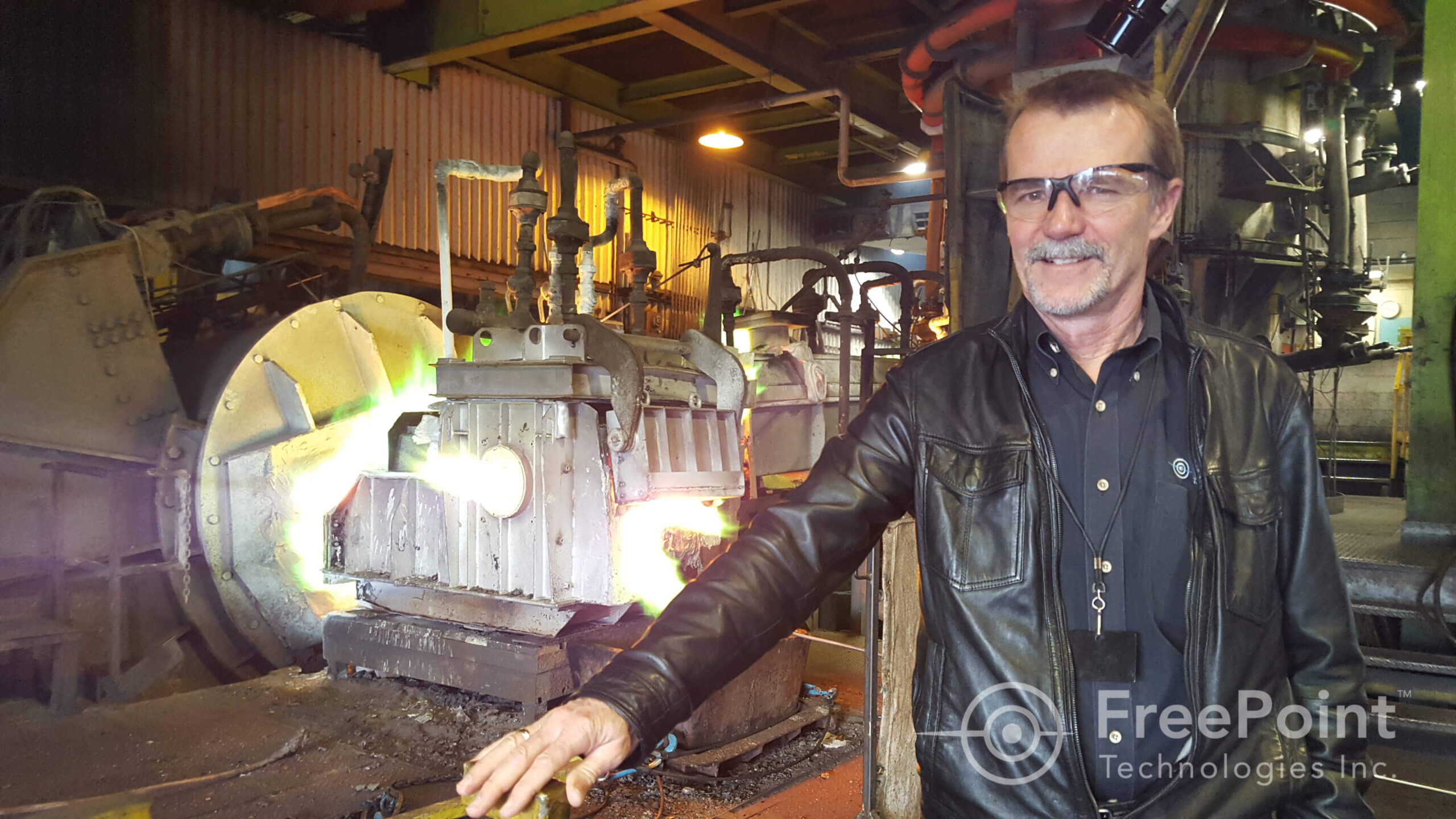
FreePoint Technologies
FreePoint Technologies (FreePoint) is a technology firm located in London, Ontario. Established in 2013, FreePoint helps industrial and manufacturing firms join the Industrial Internet of Things (IIOT) revolution. They do this with their unique, “machine wearable” technology that connects machinery to the cloud, allowing for simple collection and analysis of data on existing machinery.
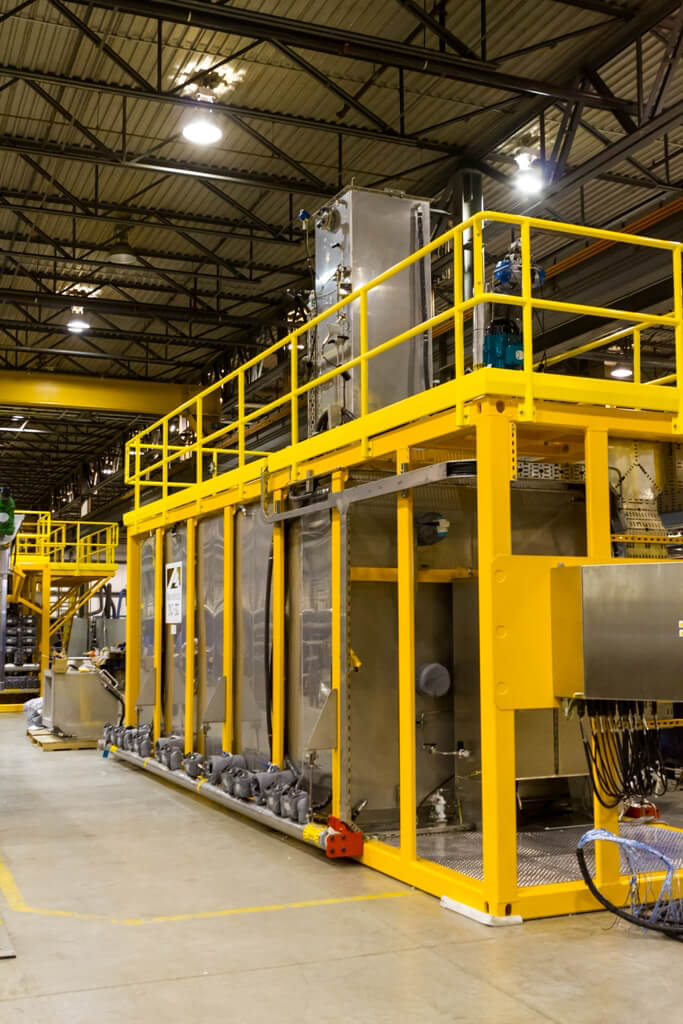
Abuma Manufacturing Limited
Abuma Manufacturing Ltd (Abuma) is a Build-to-Print metal fabricator capable of manufacturing custom components. Abuma fabricates the metal components and upper-level assemblies and integrates additional outside services like surface coatings, electrical, pneumatics, and purchased equipment as required.
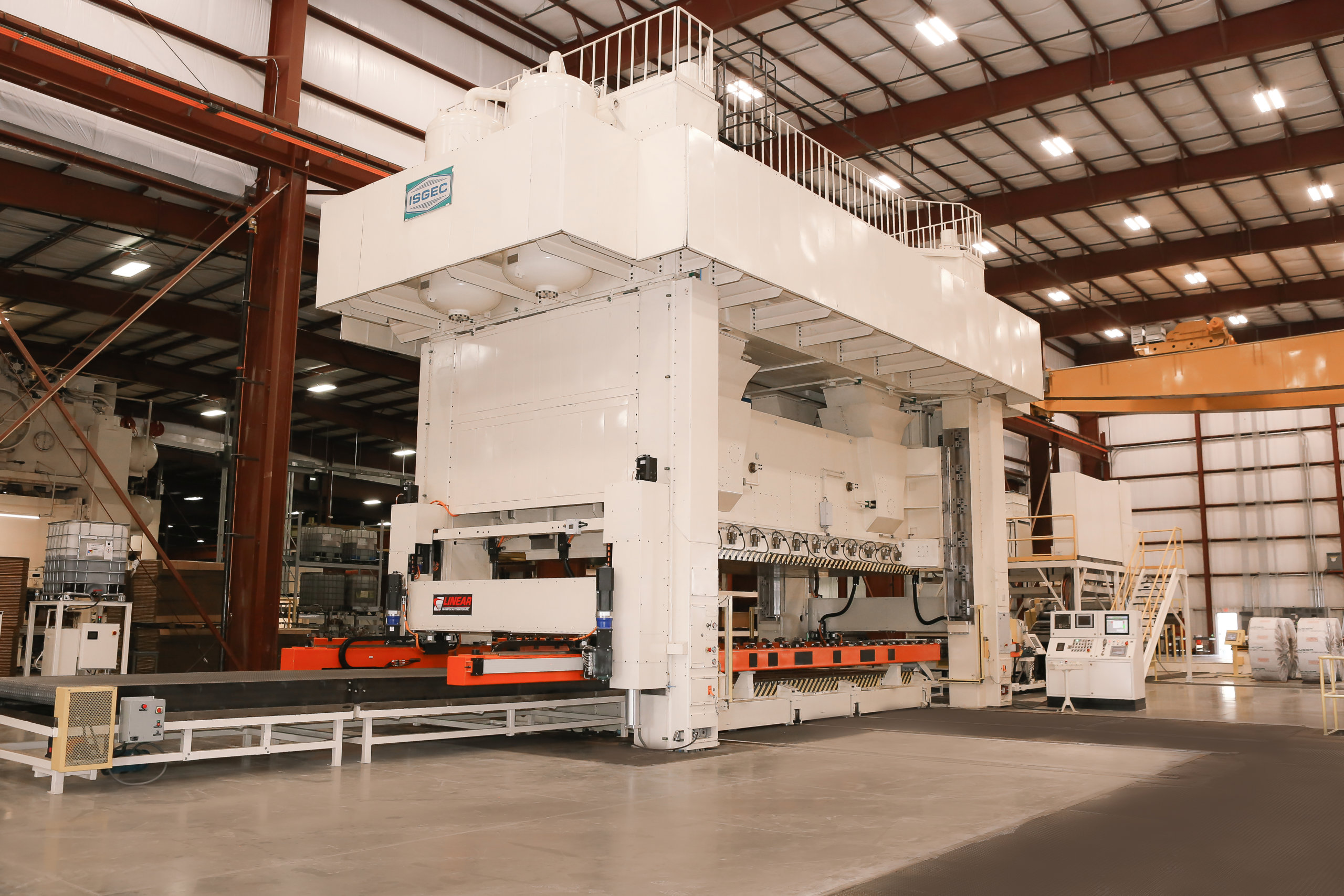
Linear Transfer Automation
Based in Barrie, Ontario, Linear Transfer Automation is a global supplier of press transfer automation, blank feed systems, and press-to-press automation. Linear is able to customize its automation solutions to fit specific equipment geometry and requirements for customers.
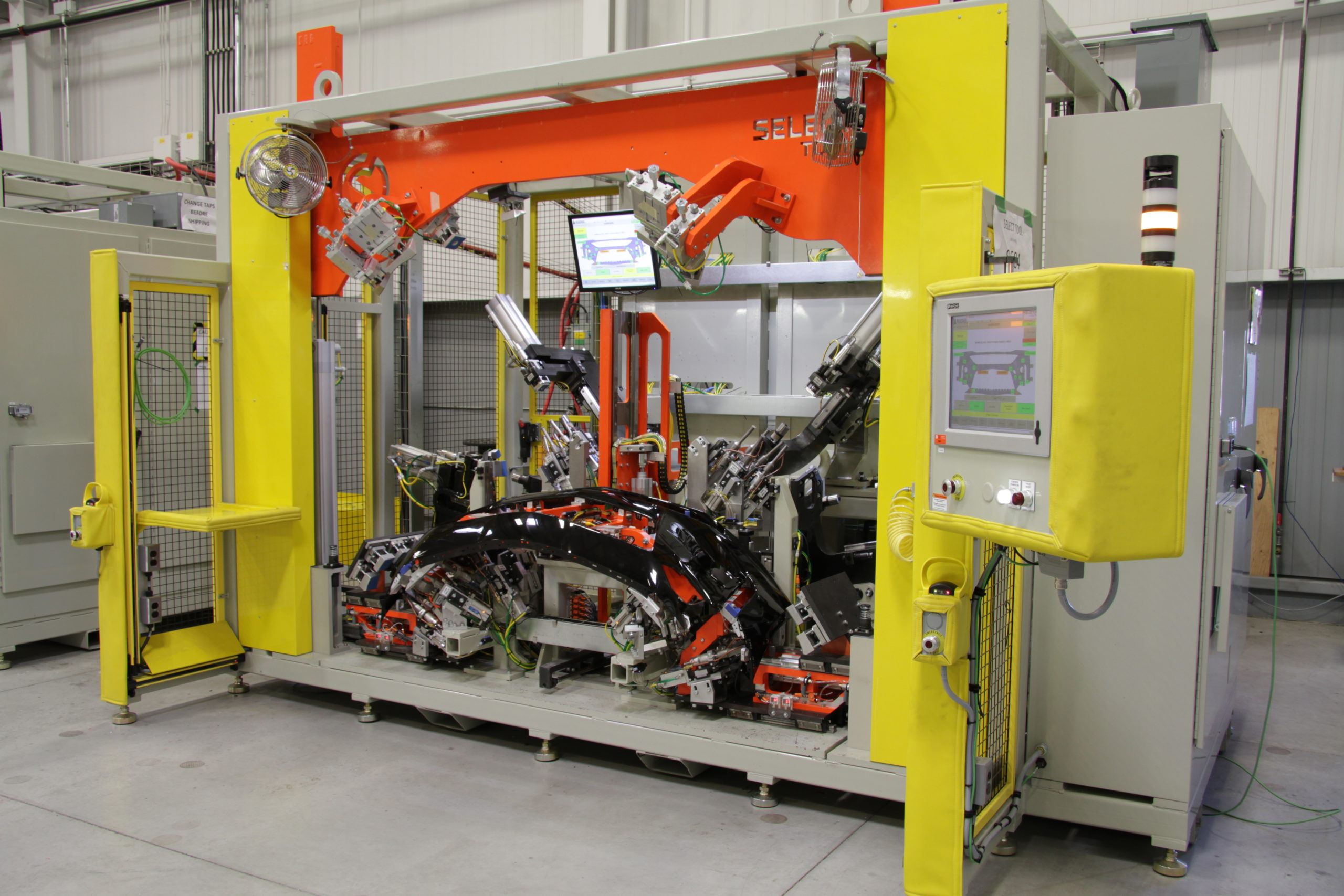
Select Tool Inc.
Select Tool is a manufacturer that has developed a reputation for providing high quality full-service gauges, fixtures, automation, and specialty tooling for the automotive, aerospace, and transportation industries.
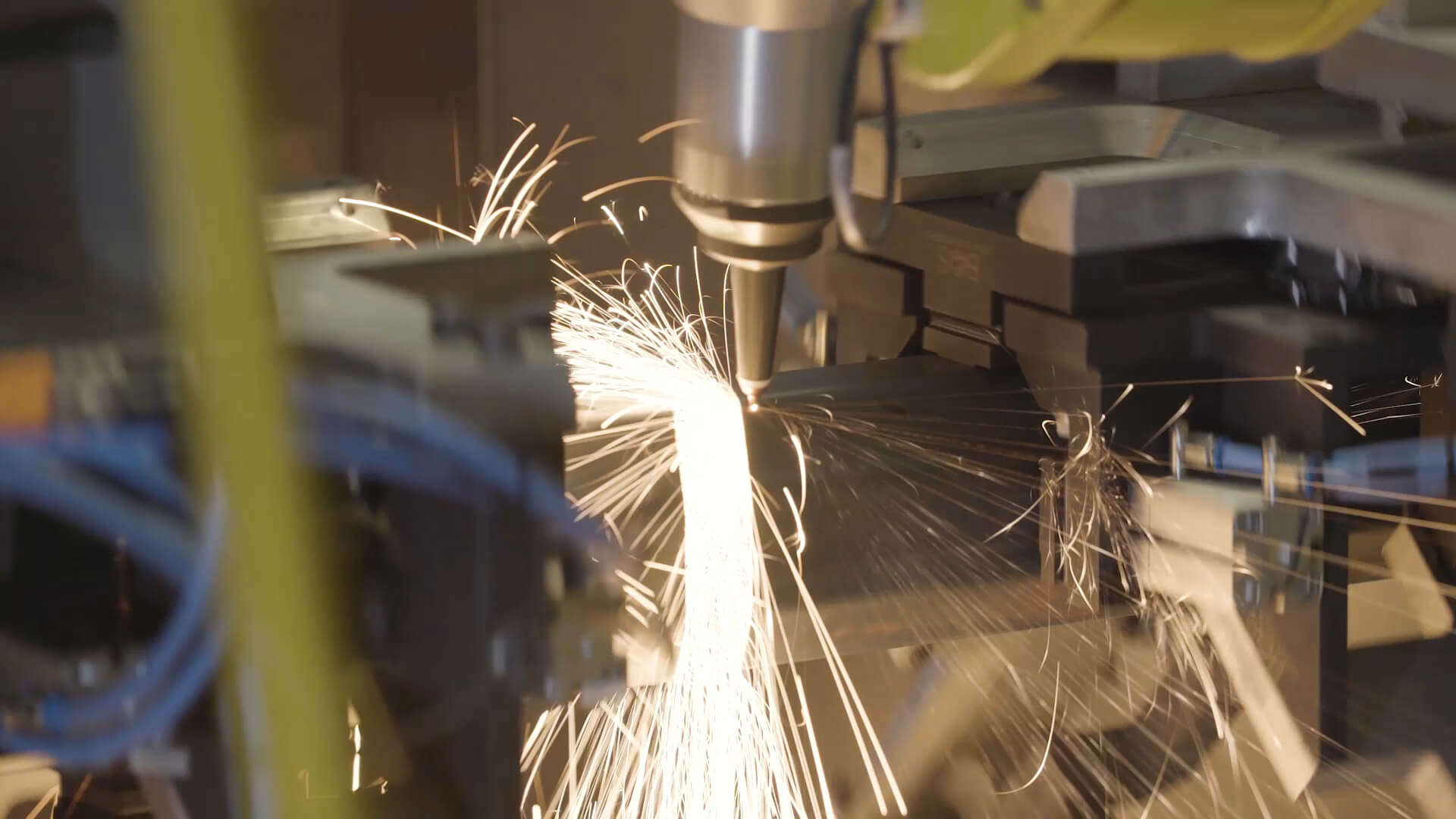
BOS Innovations
BOS Innovations develops custom factory automation solutions to help companies reach greater levels of productivity and profitability. The company’s mission is to advance North American manufacturing through world class integration of automation systems with innovative engineering, build quality, and service.