-
Headquarters -
115 Mary St, Aurora, ON, L4G 1G3
-
Year established -
1987
-
NAICS -
326193 - Motor vehicle plastic parts manufacturing
-
Major expansions -
2016
-
Employees -
500
-
Exports -
U.S., Mexico, Italy
-
Download -
Axiom Group Inc.
Axiom Group Inc. has a long history of forward-thinking and technological innovation. When Industry 4.0 presented opportunities to further improve operations, they were ready.
When Perry Rizzo, Chief Executive Officer of Axiom Group, finds a product that doesn’t meet his standards of quality and utility, he designs and makes his own. For example, when he couldn’t find an off-the-shelf solution to monitor Axiom’s manufacturing equipment 24-hours a day, the company built one from scratch. Then, he went on to refine, produce, and market that solution to his industry colleagues. Closer to home, when he couldn’t find a container that would keep his children’s soup hot and sandwich cold, he made one – and has since sold thousands of units globally. Making things, solving problems, and improving on other people’s ideas is baked into Rizzo’s DNA and – by extension, the Aurora-based thermoplastic injection molding company he founded in 1987.
Axiom Group has two core lines of business. One involves manufacturing thermoplastic injection molded components and assemblies for automotive customers – Axiom calls this the “shoot and ship” segment of their business. The company also provides engineering services including product design, prototype development, manufacturing feasibility and optimization, assembly and testing and validation to customers across the globe. Axiom’s mission is to offer the highest quality product, the greatest technical support, and the most valuable option in the marketplace.
Axiom supplies most major vehicle manufacturers as well as Tier One and Tier Two automotive parts makers. Tesla, Volkswagen, Stellantis (formerly FCA), Brose, and Multimatic are among Axiom’s largest customers.
In addition to three York Region locations (two in Aurora and one in Markham), the company has plants in Italy and Mexico. The Aurora headquarters is an 80,000 square foot facility that houses injection molding machines and vertical presses. Aurora is also home to the company’s Intex Tooling Technologies division which builds molds and develops software, including the Smart Attend monitoring system used by both Axiom and Smart Attend customers. The company employs about 500 people globally including 350 people across its Aurora locations.
Axiom supplies most major vehicle manufacturers as well as Tier One and Tier Two automotive parts makers. Tesla, Volkswagen, Stellantis (formerly FCA), Brose, and Multimatic are among Axiom’s largest customers. A visit to Axiom’s website demonstrates the breadth of its product offering. ‘Exploded’ images of automobiles show Axiom-made parts throughout the vehicle interior and exterior. Examples include Class A appearance components like interior trim panels and exterior grill covers. Axiom holds patents on a number of these components.
In 2014, Perry Rizzo was tired of finding that machines that were expected to run overnight stopped at 3 am. He wanted to know what his production systems were doing before walking into the plant in the morning. His search for commercially available production monitoring systems was unsatisfactory. He wanted to be able to collect and analyze data that would tell him cycle time, downtime, the number of parts made, issues and alarms, and any impact on production. To do so, Axiom’s engineers developed Smart Attend, a production monitoring and business intelligence system. Smart Attend allows users to run their plants at all hours of the day, anywhere in the world using precise data on how machines are performing. Originally designed for internal use, Axiom has since commercialized Smart Attend, offering manufacturers tools to reap the benefits of Ontario Made Industry 4.0 technologies.
Electric vehicle (EV) manufacturing is an important market segment for Axiom. Currently, more than one quarter of the parts and components manufactured by Axiom end up in EVs, including several Tesla models.
Axiom’s solution engineering and design services are important contributors to the company’s revenues. Manufacturing costs, both labour and raw materials, are rising, and international competition adds to the pressure faced by the injection molding business. The engineering and design services segment provides higher margins because it is a relationship-based business where Axiom can provide value-added services that improve quality and lower costs. Engineering teams are located around the world to respond to customers’ needs for efficient solutions.
Smart Attend’s General Manager, Max Preston, describes how data-driven, 24 / 7 production monitoring systems are not the only examples of innovation at Axiom. Like many companies, Axiom was affected by the pandemic as customers’ operations were forced to temporarily shut down. To preserve some level of cash flow, it retooled to make high quality, durable face shields sold at such large retailers as Costco and London Drugs. Axiom’s face shield was one of the few selected to be used in the vaccine rollout because of its quality and durability. While sales have leveled out, the company is happy to have contributed to the vaccine effort.
Axiom is proud to be part of a partnership of four companies awarded $3.5 million in funding from Next Generation Manufacturing Canada (NGen, the Advanced Manufacturing Supercluster).
Electric vehicle (EV) manufacturing is an important market segment for Axiom. Currently, more than one quarter of the parts and components manufactured by Axiom end up in EVs, including several Tesla models. These include under-the-hood and HVAC components that play an important role in the propulsion systems of these vehicles. Axiom views EVs as an important growth segment, and believes that it has developed the capability to help Canada position itself as a leader in EV manufacturing, engineering, and R&D.
Axiom is proud to be part of a partnership of four companies awarded $3.5 million in funding from Next Generation Manufacturing Canada (NGen, the Advanced Manufacturing Supercluster). The project’s goal is to develop technology that will eliminate visual transitions between different plastic materials, typically hard and soft plastics, used in automotive interiors and exteriors. In addition to benefiting the automotive industry, the technology is expected to have applications in aerospace, medical devices, construction, heavy equipment, and sporting goods manufacturing. Axiom hopes that this initiative will give the company significant competitive advantage by capturing additional market share for vehicle components.
As Axiom considers the future of vehicle manufacturing, it is constantly thinking about the workforce of the future. It believes that investing in continuous training and education is critical. It sponsors the Aurora High School Aurobots robotics team, supporting students interested in pursuing studies in science, technology, engineering and math.
Given the aggressive electric vehicle targets that many countries are setting, the students who are building robots for high school competition today can expect to see more and more electric vehicles by the time they enter the workforce. Axiom hopes these students, and many others, will consider a career in robotics engineering and related fields to be part of this exciting trend. Rizzo’s willingness to build something better than what currently exists has helped Axiom grow into an award-winning global manufacturing and solution engineering company. He is hoping the up and coming generation of engineers will share his curiosity and dedication to quality.
For more information about Axiom Group Inc., visit their website.
Published: April 22, 2021
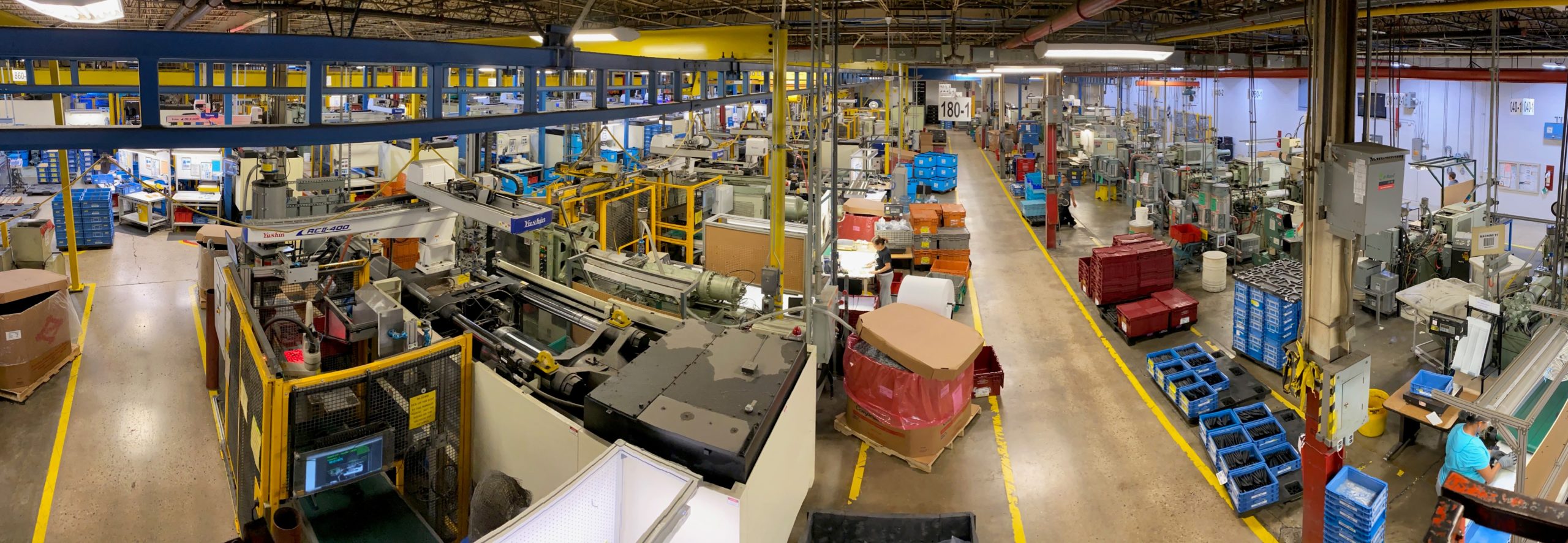
MVA Stratford
MVA Stratford Inc. is a manufacturer of custom plastic injection molded components. The firm has acquired customers from a diverse range of industries and developed strong, long-term relationships with its Tier 1 automotive customers.
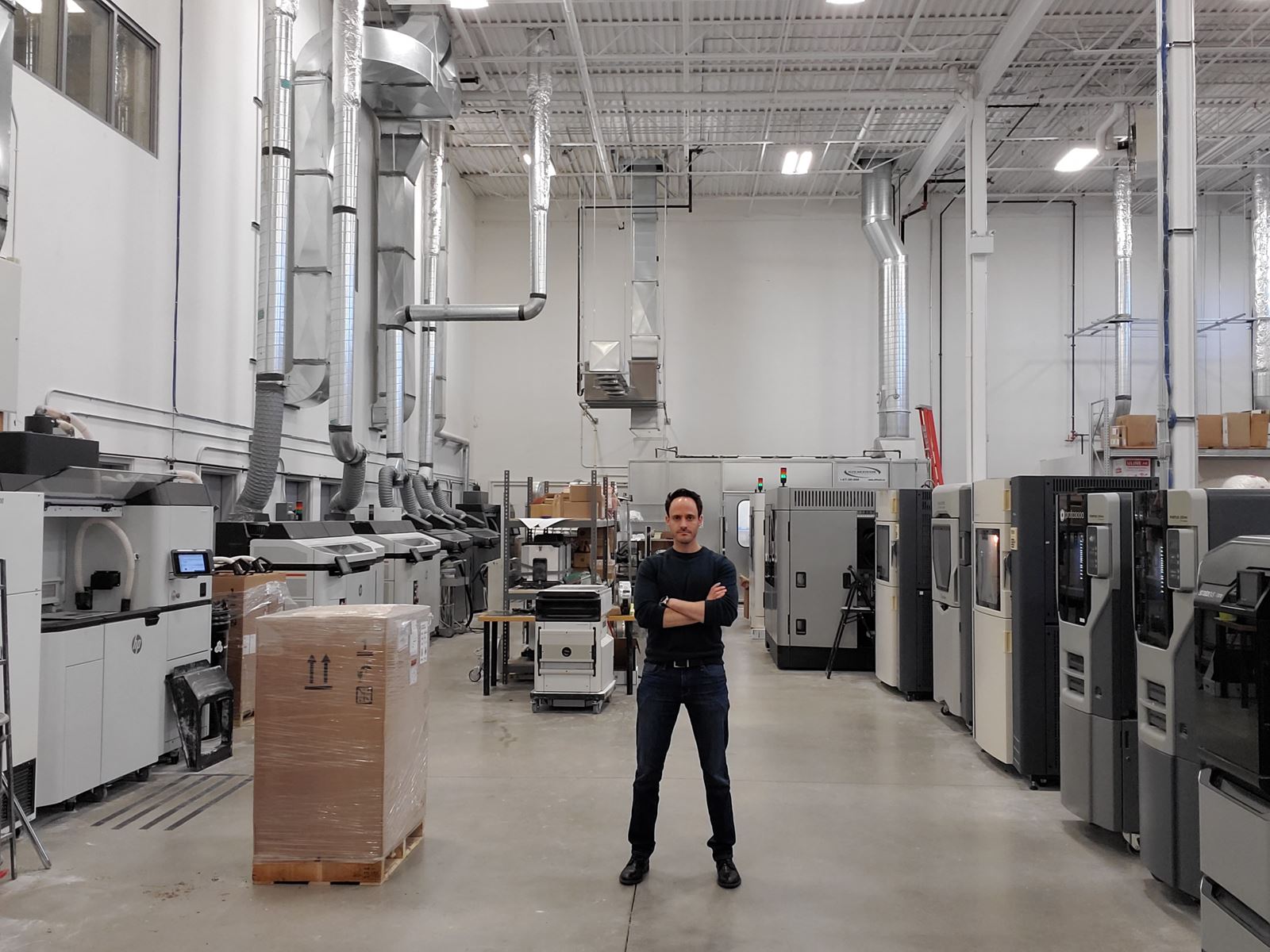
Proto3000
Based in Vaughan, Proto3000’s design, additive manufacturing, and metrology technologies help customers solve complex engineering and manufacturing challenges, resulting in shorter cycle times, more flexible supply chains, faster prototyping and more efficient production.